Автобус встречается в нашей жизни практически каждый день. Это и рейсовый городской, и небольшой пригородный, и красавец междугородний. При всех своих положительных качествах, современные автобусы проигрывают своим предшественникам в изяществе внешних форм. Если попытаться сделать современный автобус из тарных дощечек, то это будет параллелепипед, поставленный на колёса. Поэтому в качестве прототипа для модели автобуса выбран ещё недавно бегавший по нашим дорогам ЛАЗ, отличавшийся кузовом обтекаемой формы. Изготовить его из плоских дощечек не так сложно, как может показаться на первый взгляд.
В отличие от предыдущих моделей, работу начинаем сразу с корпуса. На начальном этапе он должен представлять собой прямоугольную коробку без дна с внешними размерами 100 х100 х365 мм (с учётом припусков на обработку). Стенки коробки набираются и склеиваются из подготовленных дощечек. Чтобы разнообразить монотонность больших по площади бортов кузова, можно применить для верхней и нижней его частей дерево различной структуры или цвета, например бук и осину. Поскольку впереди, в районе лобового стекла, кузов имеет скошенную поверхность, то толщину передней панели нужно увеличить до 16-20 мм, подклейкой изнутри коробки дополнительных дощечек. Теперь нужно заполнить четыре внутренних трёхгранных угла коробки деревянными кубиками. Для двух задних углов — кубики с ребром 30 мм, для передних — 15 мм. Оставшиеся восемь двухгранных внутренних углов заполняются рейками прямоугольного или треугольного (с прямым углом) сечения (на чертеже показаны пунктиром). Всё это необходимо для того, что бы после скругления внешних углов коробка кузова не имела щелей, да и попросту не развалилась на отдельные элементы. При этом обязательно надо учитывать, что клеевые швы после шлифовки окажутся снаружи. И, чтобы не испортить внешний вид модели, все стыкуемые поверхности нужно тщательно подогнать друг к другу, добиваясь минимальной толщины швов. На этом этапе желательно разметить и выпилить колёсные арки и просверлить сквозные отверстия в передней панели для установки головных фар. Возможные сколы и рваные края отверстий снимутся при последующей шлифовке.
Теперь коробку корпуса можно грубо обработать ножовкой и рубанком и отшлифовать наждачной бумагой. При этом надо учитывать, что слой снимаемого материала сравнительно большой, к тому же получить вручную правильные радиусы 135 мм и 165 мм достаточно трудно. Сделать это можно с помощью простого самодельного приспособления.
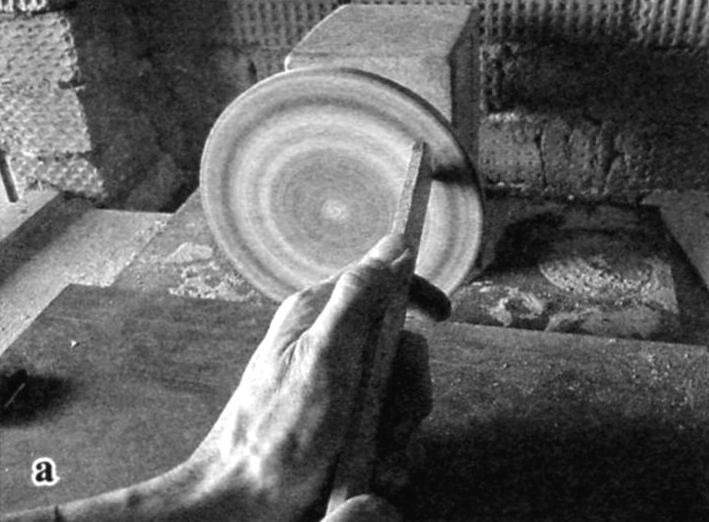
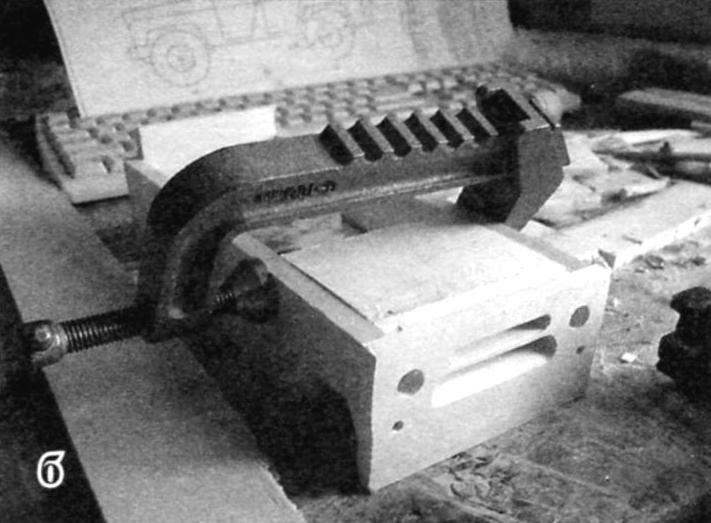
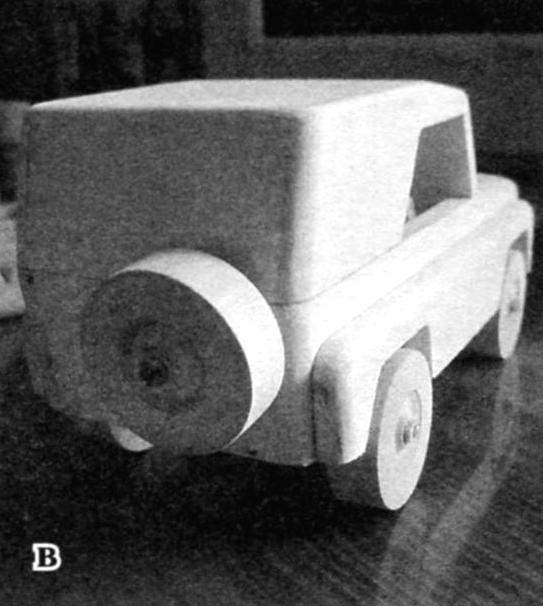
Некоторые операции процесса изготовления модели:
а) шлифование заготовки; б) склеивание деталей в конструкцию; в) готовая модель
Для начала нужно изготовить простейший шлифовальный станок (он не раз ещё пригодится в дальнейшем) — это электродвигатель мощностью 80 — 150 Вт с насаженным на вал плоским диском диаметром 120 — 180 мм из фанеры толщиной 8-12 мм, оклеенным шкуркой. На валу он закрепляется с помощью фланца так, чтобы сторона диска с наклеенной шкуркой не имела выступающих элементов. В качестве привода можно применить и электродрель. Привод надо закрепить на каком-либо основании. Для этого удобно использовать обрезки ламинированных древесностружечных плит. Также на основании закрепляются два упора, которые должны быть съёмными, чтобы можно было регулировать их положение относительно шлифовального диска. В качестве упоров можно применить небольшие струбцины. Упоры ограничивают перемещение плиты, на которой закрепляется заготовка корпуса. Плита свободно скользит по основанию, поэтому лучше использовать ламинированные ДСП. Перемещение плиты ограничивается только установленными упорами. Корпус автобуса закрепляется на плите шурупом, который является осью вращения, и обеспечивает нужный радиус обработки. Для этого внутрь корпуса временно вклеивается брусок.
При вращающемся шлифовальном диске плита вместе с корпусом постепенно придвигается к кругу, при этом корпус надо поворачивать вокруг оси-шурупа, снимая постепенно лишний материал. Когда плита дойдёт до упоров — обработка закончена. При этом автоматически выдерживается необходимый радиус кривизны. Аналогично осуществляется обработка задней части корпуса. Для обработки наклонной поверхности лобового стекла под плиту устанавливается клиновидная подкладка. Малые радиусы скругления углов можно выполнить, не закрепляя корпус шурупом. После такой обработки получается практически готовый корпус автобуса, требующий лишь минимальной доработки шкуркой вручную.
Для рамы выбирается подходящая дощечка толщиной 8 мм. Рама вклеивается несколько заглублено относительно нижнего обреза корпуса. Для этого с внутренней стороны передней и задней стенок корпуса в соответствующих местах приклеиваются упоры, сделанные из обрезков реек, так чтобы рама после установки ложилась на них. Теперь остаётся закрепить вентиляционные люки на крыше, фары, мосты с колёсами. Мосты делаются из круглых или прямоугольных в сечении брусочков, с продольными отверстиями для осей, приклеенных к раме. Передний бампер и воздухозаборник на заднем скате корпуса можно выгнуть из распаренных тонких дощечек или выпилить лобзиком по контуру из заготовки нужной толщины и приклеить на соответствующие места.
Д. КАЛЮЖНЫЙ, г. Ижевск
Рекомендуем почитать
ГИДРАВЛИКА ВМЕСТО ТРАНСМИССИИ
Ни остродефицитного дифференциала, ни планетарного механизма поворота, практически недоступного для самоделыциков, ни сложных в изготовлении обгонных муфт не требуется для этого...
Шлюпки «на потоке»
При постройке копий военных кораблей и торговых судов всегда есть необходимость в изготовлении макетов шлюпок. К сожалению, многие моделисты относятся к этому без должного уважения. И в...