Сьогодні можна сміливо стверджувати: хочеш отримати добрий результат на змаганнях — використовуй двигун із «кольоровою» парою поршень — циліндр! Підтвердження тому – «кольорова» начинка мотоустановок моделей – призерів чемпіонатів найвищого рангу.
Знаючи про безперечні переваги таких двигунів, багато хто береться за самостійне виготовлення нових пар. І відразу ж стикаються з безліччю труднощів, невідомих факторів та величин. Їх — розповідь майстра спорту СРСР Ю. Муссалитина про нанесення хромового покриття деталі з різних металів.
Хромування, одне з найнеобхідніших двигуністів покриттів, відноситься до найбільш трудомістких процесів гальванотехніки. Воно вимагає особливої ретельності та дотримання чистоти як при приготуванні електроліту, так і самих речовин, що входять до його складу. Вода використовується дистильована або (лише в крайньому випадку!) ґрунтовно прокип’ячена.
ПОЧНІТЬ З ВАННИ
Заняття модельною гальванотехнікою почніть із виготовлення ванни. Насамперед підберіть каструлю на 10 л і трилітрову скляну банку. Місткості меншого розміру краще не застосовувати – це може ускладнити регулювання параметрів процесу, та й при наведених величинах об’єму ванни вистачає лише для хромування 6-8 гільз циліндрів.
Склеївши з 1-1,5 мм фанери корпус, зберіть ванну згідно з наведеним малюнком і закрийте все фанерним кільцем. Робота над ванною закінчується виточуванням кришки каструлі та монтажем на ній ТЕНів та контактного градусника.
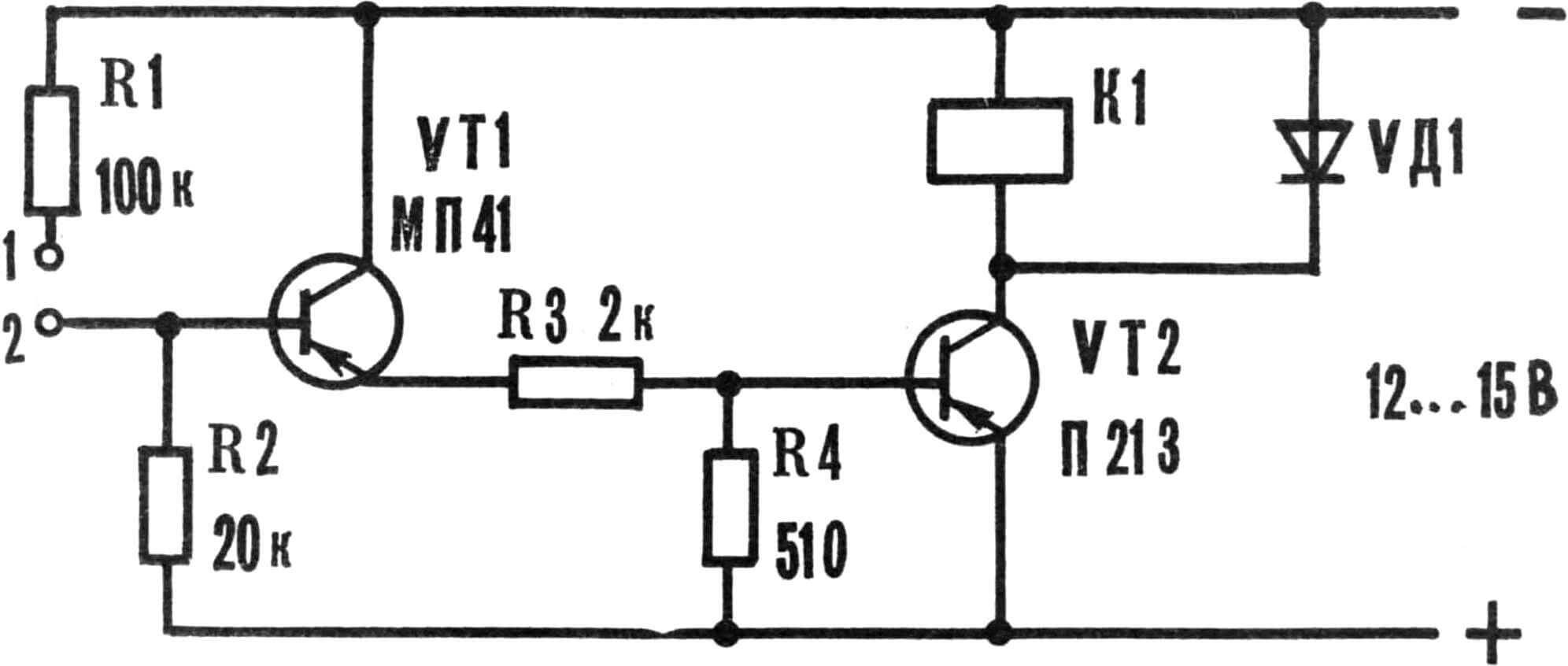
Тепер – електроустаткування. Для живлення ванни можна використовувати будь-яке джерело постійного струму з підключеним на виході електролітичним конденсатором 80 000 мкф X 25 В. Провід живлення повинен мати переріз не менше 2,5 мм 2 . Регулятором сили струму, що замінює регулятор напруги, може бути секційний реостат. Він включається послідовно з гальванічною ванною і складається з паралельних, які включаються однополюсними рубильниками секцій. Кожна наступна має опір удвічі більший за попередній. Число таких секцій 7-8.
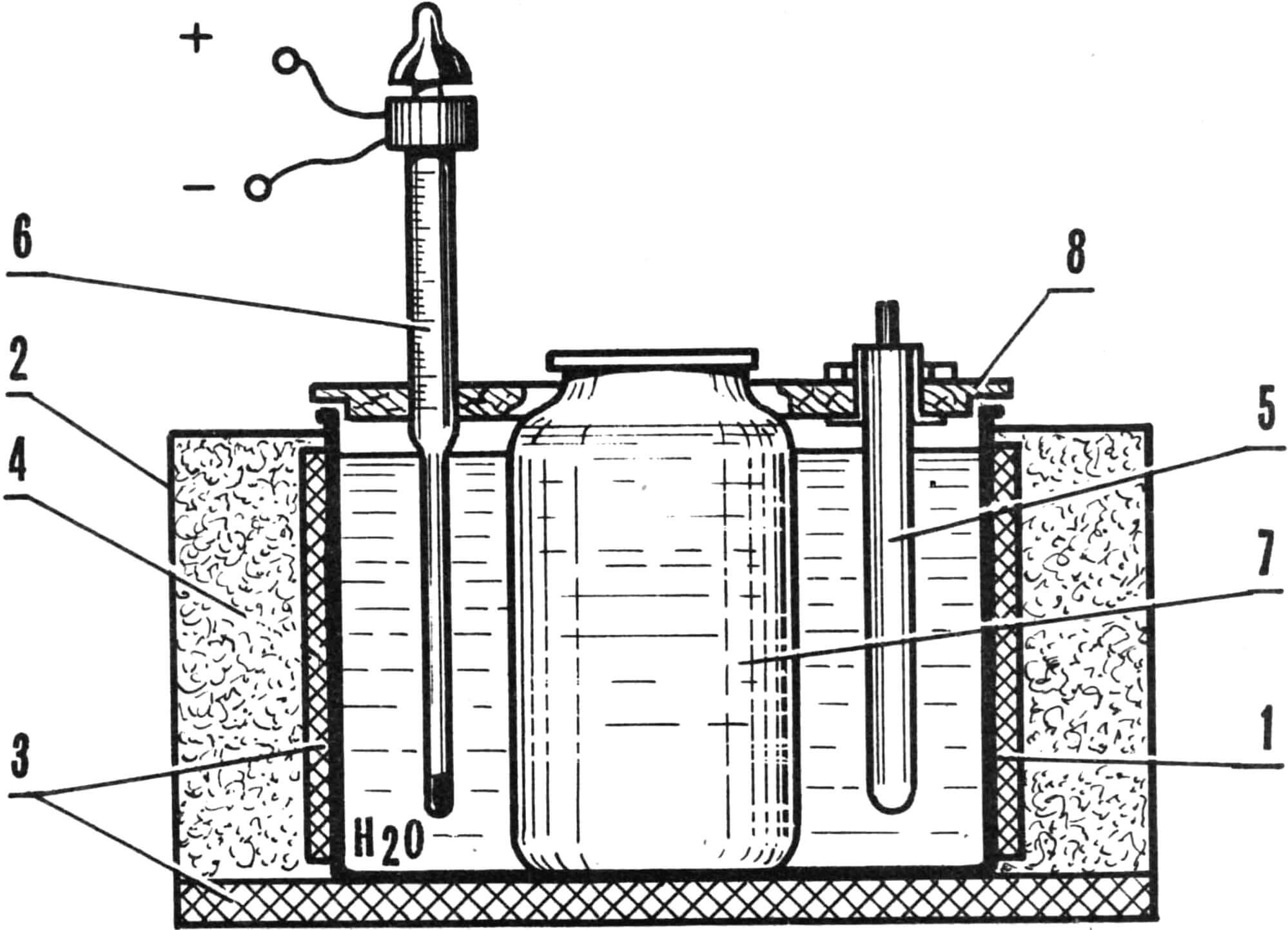
1 — внутрішній корпус (каструля об’ємом 10 л), 2 — корпус (фанера товщиною 1—1,5 мм), 3 — теплоізоляція (склотканина), 4 — теплоізолюючий шар (азбестова крихта, пісок, скловата), 5 — трубчастий електронагрівник ТЕНнік, 6 (Банку), 8 – кришка (дельта-деревина).
На передній панелі блока живлення встановіть дві розетки на 15 А, одну нормальної полярності, іншу зворотної. Це дозволить швидко провести анодну обробку деталі та перейти на хромування простим переставлянням вилки. Розетки з трьома виходами, щоб не помилитися в полярності (підключаються, звичайно, лише два гнізда).
Для підтримки постійної температури електроліту ванна забезпечується контактним градусником. Безпосередньо керувати роботою ТЕНів він не може через великі струми, тому потрібно зібрати нескладний пристрій, схема якого наведена на малюнках. Деталі терморегулятора: транзистори МП13-МП16, МП39-МП42 (VT1); 213-217 (VT2) з будь-якими літерними позначеннями; резистори МЛТ-0,25, діод-Д226, Д202-Д205; реле – ТКЕ 52 ПІДГ або ОКН паспорт РФ4.530.810.
Налагодження терморегулятора: якщо при закорочуванні точок 1-2 реле не спрацьовує, з’єднують емітер та колектор VT1. Увімкнення реле вказує на несправність або малий коефіцієнт посилення VT1. В іншому випадку несправний транзистор VT2 або має недостатній коефіцієнт посилення.
Зібравши та налагодивши пристрій ванни, можна приступати до приготування електроліту. Для цього необхідно:
– Налити в банку трохи більше половини підготовленої дистильованої води, підігрітої до 50 °,
– Засипати хромовий ангідрид і розмішати,
– Долити воду до розрахункового обсягу,
– Влити сірчану кислоту,
– Пропрацювати електроліт 3-4 год з розрахунку 6-8 А г / л.
Остання операція потрібна для накопичення невеликої кількості іонів Cr3 (2-4 г/л), присутність яких сприятливо впливає на процес осадження хрому.
СКЛАДИ ЕЛЕКТРОЛІТІВ
Хромовий ангідрид – 250 г/л або 150 г/л
Сірчана кислота – 2,5 г/л або 1,5 г/л
НЕ ЗАБУДЬТЕ ПРО РЕЖИМИ ХРОМУВАННЯ!
Процес хромування сильно залежить від температури електроліту і щільності струму. Обидва фактори впливають на зовнішній вигляд і властивості покриття, а також вихід хрому по струму. Необхідно пам’ятати, що з підвищенням температури вихід струму знижується; з підвищенням щільності струму вихід струму зростає; при нижчих температурах і незмінною щільності струму виходять сірі покриття, а за підвищених — молочні. Практичним шляхом знайдено оптимальний режим хромування: щільність струму 50-60 А/дм 2 за температури електроліту 52° – 55° ±1°.
Щоб бути впевненим у працездатності електроліту, у приготовленій ванні можна покрити кілька деталей, подібних за формою та розмірами до робочих зразків. Підібравши режим і дізнавшись вихід струму простим виміром розмірів до і після хромування, можна приступати до покриття гільз.
За запропонованою методикою накладають хром на сталеві, бронзові та латунні деталі. Підготовка їх полягає у промиванні поверхонь, що підлягають хромуванню, бензином і потім милом (за допомогою зубної щітки) у гарячій воді, зарядці в оправку та розміщення у ванні. Після занурення в електроліт потрібно почекати 3-5 сек і потім включити робочий струм. Затримка потрібна у тому, щоб деталь прогрілася. Одночасно відбувається активування поверхні деталей з латуні та міді, оскільки ці метали добре труїться в електроліті. Однак більше 5 секунд чекати не слід — у складі цих металів є цинк, присутність якого в електроліті неприпустима.
ХРОМУЄМО АЛЮМІНІЄВІ СПЛАВИ
На процесах нанесення хрому на алюмінієві сплави необхідно зупинитися особливо. Виконання таких покриттів завжди пов’язане із низкою труднощів. Насамперед це необхідність попереднього нанесення проміжного шару.
ВИЗНАЧЕННЯ ЗМІСТ ХРОМОВОГО АНГІДРИДУ CrO 3 В ЗАЛЕЖНОСТІ ВІД ПІДІЛЬНОЇ ТЕРЕЗИ РОЗЧИНУ
Питома вага за 15° | Зміст CrO 3 в молях | Зміст CrO 3 в г/л |
---|---|---|
1,07 | 1,00 | 100 |
1,08 | 1,14 | 114 |
1,09 | 1,29 | 129 |
1,10 | 1,43 | 143 |
1,11 | 1,57 | 157 |
1,12 | 1,71 | 171 |
1,13 | 1,85 | 185 |
1,14 | 2,00 | 200 |
1,15 | 2,15 | 215 |
1,16 | 2,29 | 225 |
1,17 | 2,43 | 243 |
1,18 | 2,57 | 250 |
1,19 | 2,72 | 272 |
1,20 | 2,88 | 288 |
1,21 | 3,01 | 301 |
1,22 | 3,16 | 316 |
1,23 | 3,30 | 330 |
1,24 | 3,45 | 345 |
1,25 | 3,60 | 360 |
1,26 | 3,75 | 375 |
1,27 | 3,90 | 390 |
1,28 | 4,06 | 406 |
1,29 | 4,22 | 420 |
1,30 | 4,38 | 438 |
1,31 | 4,53 | 453 |
1,32 | 4,68 | 468 |
Сплави алюмінію, що містять велику кількість кремнію (до 30%, сплави марок АК12, АЛ25, АЛ26, САС-1), можна хромувати таким чином:
– промивання деталі в бензині, – промивання в гарячій воді з пральним порошком або милом,
– обробка деталі в розчині азотної та плавикової кислот (відношення 5:1) протягом 15-20 с,
– Промивання в холодній воді,
– Встановлення деталі на оправці та хромування (завантаження у ванну під струмом!).
Інша річ, якщо необхідно покрити хромом сплав АК4-1. Його вдається відхромувати лише за допомогою проміжного шару. До таких методів належать: цинкатна обробка; по підшару нікелю; через сіль нікелю; через анодну обробку деталі у розчині фосфорної кислоти.
У всіх випадках деталі готують так:
– шліфування (і притирання);
– очищення (видалення жирових відкладень після шліфування в бензині або трихлоретилені, потім у лужному розчині),
– Промивання в проточній холодній і теплій (50-60 °) воді,
– травлення (для видалення частинок, що залишилися на поверхні після шліфування та притирання, а також для покращення підготовки поверхні деталі до нанесення хрому).
Для травлення використовується розчин їдкого натру (50 г/л), час обробки 10-30 при температурі розчину 70-80 °.
Для травлення сплавів алюмінію, що містять кремній та марганець, краще використовувати такий розчин, у вагових частинах:
азотна кислота (щільність 1,4)-3, плавикова кислота (50%) – 1.
Час обробки деталей 30-60 при температурі розчину 25-28 °. Після травлення, якщо це гільза циліндра, її треба негайно промити в проточній воді і на 2—3 опустити в розчин азотної кислоти (50%) з подальшим промиванням водою.
ПРОМІЖНІ ПОКРИТТЯ
Цинкування
Алюмінієві вироби при кімнатній температурі опускають на 2 хв розчин (їдкий натр 400 г/л, сірчанокислий цинк 120 г/л, сіль Рошеля 5-10 г/л. Або: їдкий натр 500 г/л, окис цинку 120-140 г/л). Покриття досить рівномірне і має сірий (іноді блакитний) колір.
Якщо цинкове покриття лягло нерівномірно, деталь опускають в 50-відсотковий розчин азотної кислоти, що натравлює, на 1-5 с і після промивання повторюють цинкування. Для магнійсодержащих сплавів алюмінію подвійне цинкування обов’язково. Нанісши другий шар цинку, деталь промивають, заряджають в оправку і під струмом (без подачі напруги цинк встигає частково розчинитися в електроліті, забруднюючи його) встановлюють у ванні. Попередньо оправлення з деталлю занурюється у склянку з водою, нагрітою до температури 60°. Процес хромування простий.
Нікелювання (хімічне)
Якщо цинк не лягає на алюміній (найчастіше це відбувається на сплаві АК4-1), можна спробувати нанести хром через нікель. Порядок роботи такий:
– Притирання поверхні,
– Знежирення,
– травлення 5-10 с в розчині азотної та плавикової кислот, змішаних у співвідношенні 3:1,
– нікелювання.
Остання операція – у розчині наступного складу: сірчанокислий нікель 30 г/л, гіпофосфіт натрію 10-12 г/л, оцтовокислий натрій 10-12 г/л, глікоколь – 30 г/л. Складається він спочатку без гіпофосфіту, що вводиться перед нікелюванням (з гіпофосфітом розчин довго не зберігається). Температура розчину при нікелюванні 96-98 °. Можна використовувати розчин і без глікоколи, тоді температура повинна бути знижена до 90 °. За 30 хв на деталь осаджується шар нікелю завтовшки від 0,1 до 0,05 мм. Посуд для робіт – тільки скляний або порцеляновий, тому що нікель осідає на всі метали восьмої групи періодичної таблиці. Добре піддаються нікелюванню латунь, бронза та інші мідні сплави.
Після осадження нікелю проводиться термообробка поліпшення зчеплення з основним металом (200—250°, витримка 1—1,5 год). Потім деталь монтується на оправці для хромування і опускається на 15 – 40 с розчин 15% сірчаної кислоти, де обробляється зворотним струмом з розрахунку 0,5-1,5 А/дм 2 . Відбувається активування нікелю, видаляється окисна плівка, і покриття набуває сірого кольору. Кислота повинна застосовуватися тільки хімічно чиста (у крайньому випадку акумуляторна). Інакше нікель набуває чорного кольору, і хром на таку поверхню ніколи не ляже.
Після цього оправлення з деталлю завантажують у ванну хромування. Спочатку дають струм вдвічі більший, потім протягом 10-12 хв його зменшують до робітника.
Дефекти хімічного нікелювання:
– нікелювання не відбувається: деталь не прогрілася, слід почекати деякий час,
– Плями на поверхні (характерно для АК4-1): погана термообробка деталі, потрібно її термообробити при 200-250 ° протягом 1,5-2 год.
Видалення нікелю з алюмінієвих сплавів можна проводити розчині азотної кислоти.
Іноді у процесі нікелювання відбувається саморозряд – випадання порошкоподібного нікелю. В цьому випадку розчин виливають, а посуд обробляють розчином азотної кислоти для видалення з її поверхні нікелю, який заважатиме осадженню на деталі.
Хотілося б відзначити, що нікель-фосфор сам по собі має дуже цікаві властивості, не властиві хромовим покриттям. Це рівномірність шару поверхні деталей (після осадження доведення не потрібно); висока твердість після термообробки (режим 400 ° протягом години дає твердість покриття HV 850-950 і більше); низький коефіцієнт тертя проти хромом; дуже незначне розширення; висока межа міцності при розтягуванні.
Нікель-фосфор без подальшого нанесення хрому може використовуватися не тільки як проміжне покриття на гільзах, але і як робоче, що знижує тертя та зношування, для золотників і поршневих пальців. Після двох років активної експлуатації двигуна з деталями подібної обробки на них була відсутня явна вироблення, характерна для сталевих гартованих поверхонь.
Нанесення хрому через сіль нікелю
Весь процес зводиться до наступного:
– травлення в розчині їдкого натру (50 г/л, t=80°, 20 с),
– Промивання в проточній воді,
– Нанесення 1-го проміжного шару (хлористий нікель, 1 хв),
– нацкування проміжного шару в розчині азотної кислоти (розчин кислоти 50%, 1 хв),
– Нанесення 2-го проміжного шару (хлористий нікель, 1 хв),
– Промивання водою,
– травлення (азотна кислота 50%, 15 с),
– Промивання в проточній воді,
– Завантаження у ванну хромування під струмом.
Нанесення хрому через анодну обробку
Замість проміжних шарів можна виконувати анодну обробку в розчині 300—350 г/л фосфорної кислоти при температурі 26—30°, напрузі на затискачах 5—10 і щільності струму 1,3 а/дм 2 . Ванну слід охолоджувати. Для сплавів, що містять мідь та кремній, застосовують розчин 150-200 г/л фосфорної кислоти. Режим – 35 °, час обробки 5-15 хв.
Після анодної обробки слід провести короткочасну катодну обробку у лужній ванні, яка частково знімає оксидний шар. Як показали дослідження, в процесі анодної обробки алюмінієвих сплавів у фосфорній кислоті на деталях утворюється шорстка поверхня, яка сприяє міцному зчепленню покриття, що наноситься згодом.
ЗАСТОСУВАННЯ, ВИПРАВЛЕННЯ
Хромування гільзи
Для виконання робіт із гільзою циліндра виготовляється оправлення. Її пристрій зрозумілий з наведеного малюнка, зупинимося лише на окремих деталях.
Анод – сталева шпилька; з одного її кінця на довжині 50-60 мм наплавляється свинець із сурмою (7-8%). Свинець проточується по зовнішньому діаметру до 6 мм (для робочих гільз Ø 15 мм). З іншого боку шпильки нарізається різьблення для фіксації дроту.
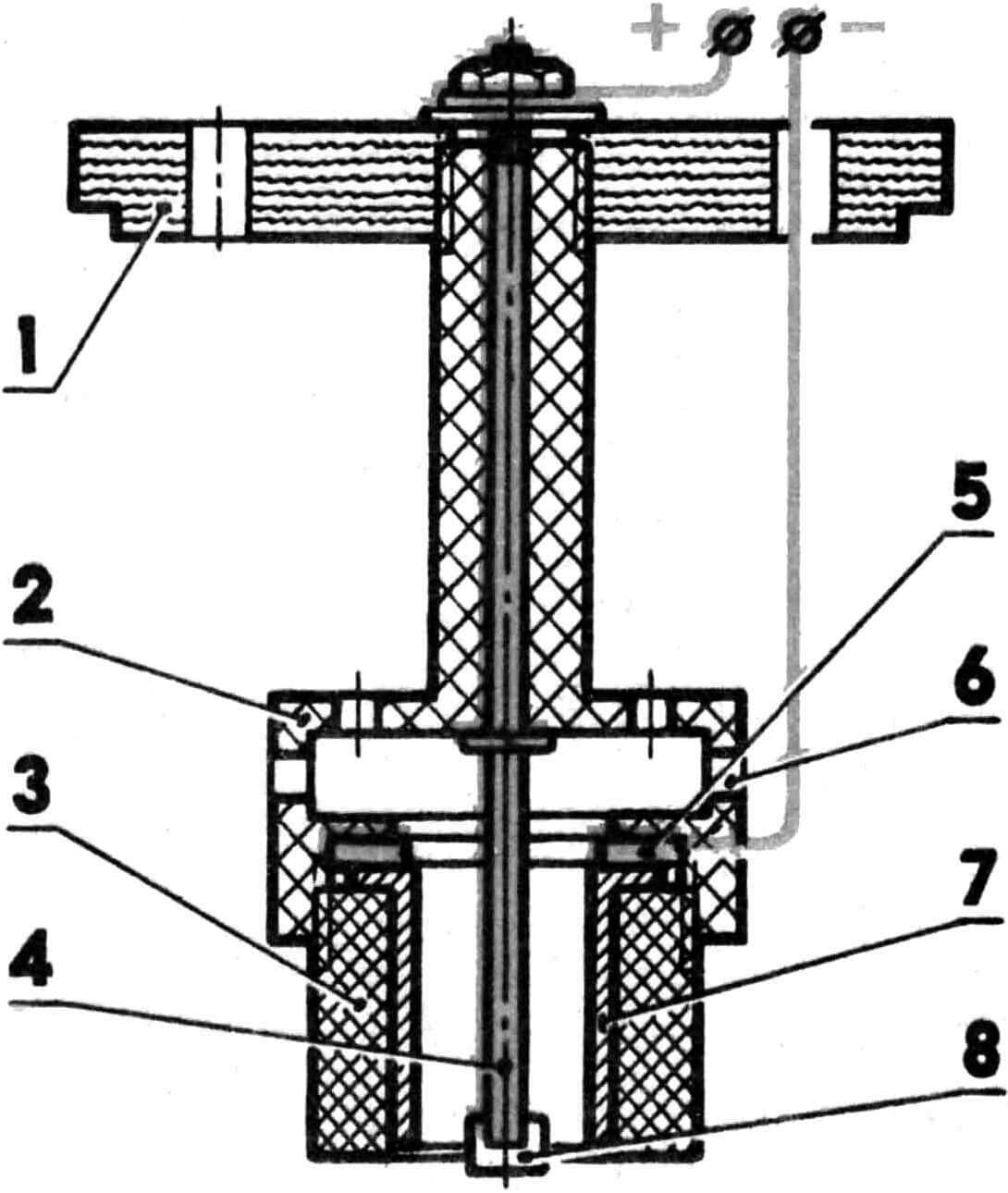
1 – кришка (вініпласт), 2 – верхня частина оправки (фторопласт), 3 – нижня частина оправки (фторопласт), 4 – анод (сталь), 5 – катод, 6 – наскрізне вікно для проходу електроліту, 7 – гільза, що покривається, 8 – насадка.
Катодом служить кільце з внутрішнім діаметром, що на 0,5 мм перевищує внутрішній розмір гільзи. У нього карбується відрізок ізольованого дроту. Мідні та латунні провідники краще не використовувати – електроліт розчиняє їх, і контакт може бути порушений. Перед монтажем виправлення у ванні корисно перевірити надійність контактів тестером.
Хромування сталевих деталей (колінвал, палець кривошипу, палець поршня, обойми підшипників)
Хромування сталевих деталей ведеться за такою технологією: видалення жирових плям за допомогою бензину,
– Промивання в гарячій воді з милом,
– Обробка деталі зворотним струмом протягом 2-3 хв,
– Переключення в режим хромування зі струмом, в 2-2,5 рази більшим за розрахунковий, і поступове зниження струму протягом 10-15 хв.
Розрахунковий струм визначається перемноженням площі поверхні, що хромується на струм процесу. Для сталі остання величина – 50 А/дм 2 . При хромуванні, наприклад, посадкового місця під корінний підшипник на колінвалі двигуна КМД-2,5 розрахунковий струм дорівнюватиме 0,03 дм2Х50 А/дм 2 = 1,5 А.
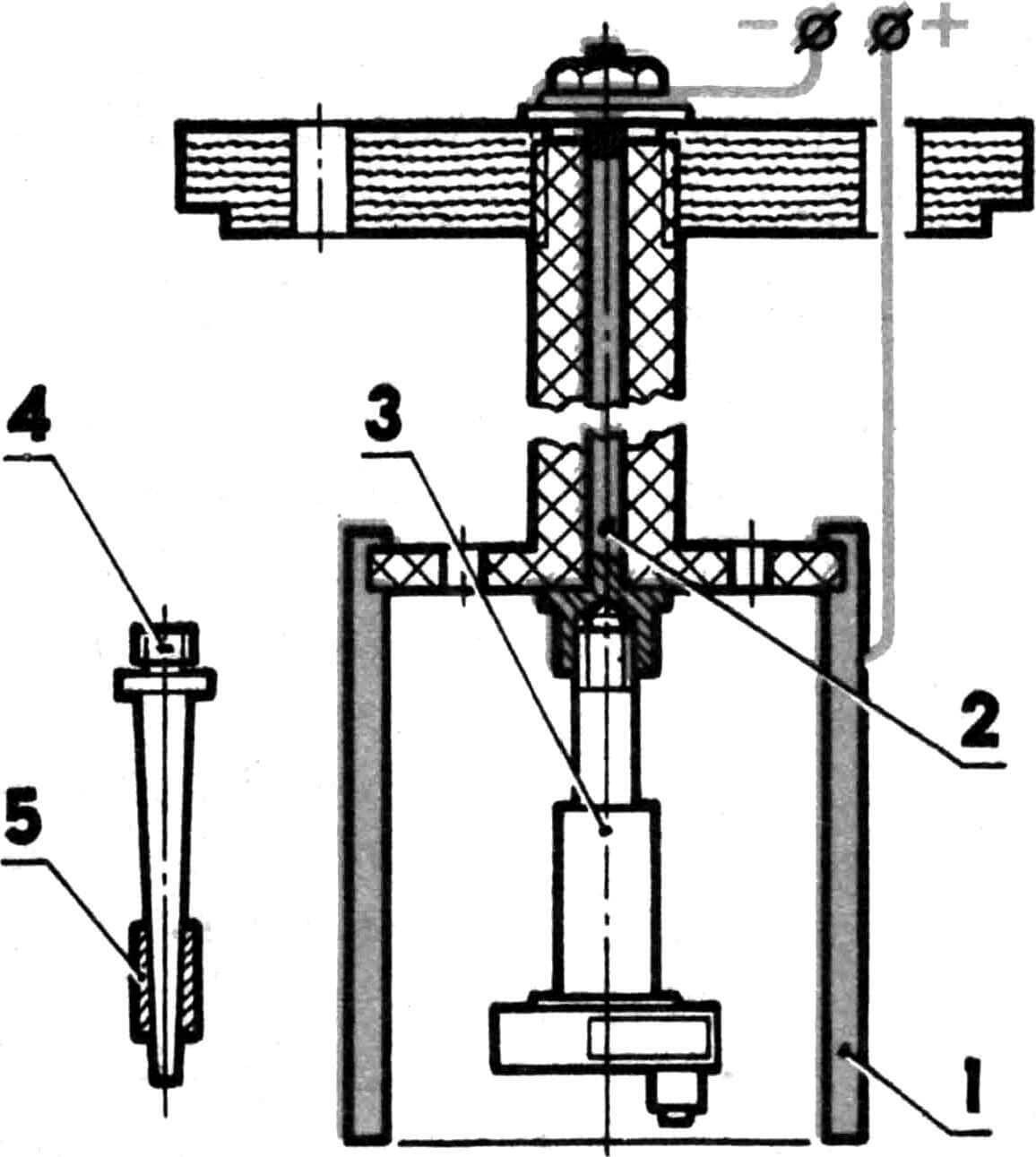
1 – анод, 2 – катод, 3 – колінвал, 4 – конусна оправка, 5 – поршневий палець.
Для хромування пальця кривошипа знадобиться нова оправка. Як і під час обробки коленвала, всі відкриті ділянки поверхні закриваються клеєм «АГО». Анод виточується зі сталі з наступним заливанням свинцем і розточуванням отвору під палець. Застосування сталевої деталі пояснюється необхідністю забезпечити надійний контакт – у свинці різьбові з’єднання ненадійні. Розрахунки струмів аналогічні. Робота проводиться у виправленні валу за допомогою спеціальної насадки.
Майже нічим не відрізняється хромування підшипників. Єдине – для запобігання внутрішній частині деталі її заповнюють солідолом або іншим консистентним мастилом, яке після нанесення покриття вимивається бензином.
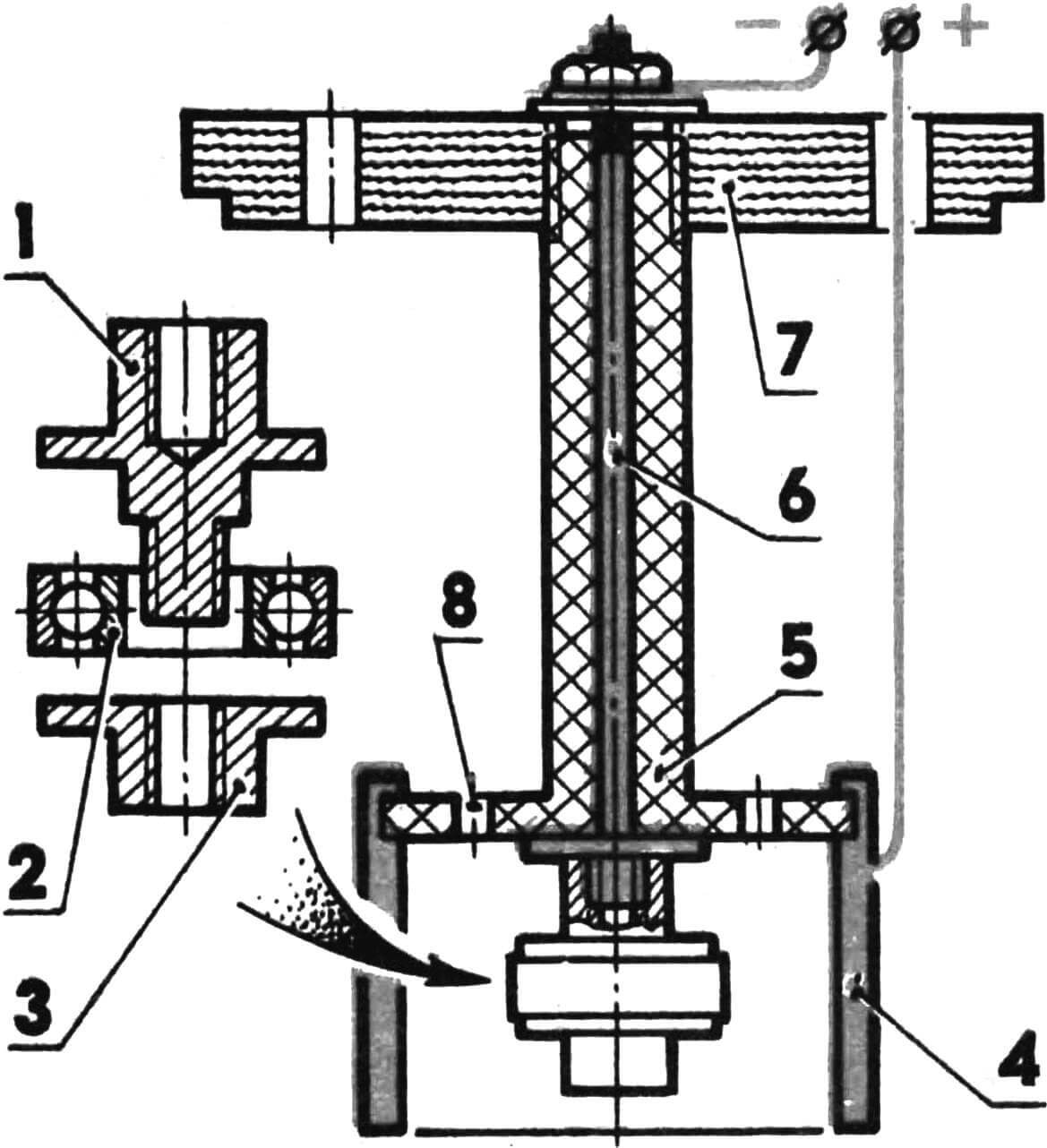
1 – корпус оправлення підшипника, 2 – шарикопідшипник, 3 – фігурна гайка, 4 – анод (свинець), 5 – центральна частина оправки для хромування, 6 – катод (сталь), 7 – кришка, 8 – наскрізне вікно для проходу електроліту.
Концентрація хромового ангідриду в електроліті контролюється ареометром. Концентрацію сірчаної кислоти вдається визначати лише, на жаль, побічно, за якістю покриття.
У процесі хромування відбувається випаровування електроліту. У цих випадках доливають воду до рівня. Робиться це без встановлення деталей – можлива зміна температури електроліту.
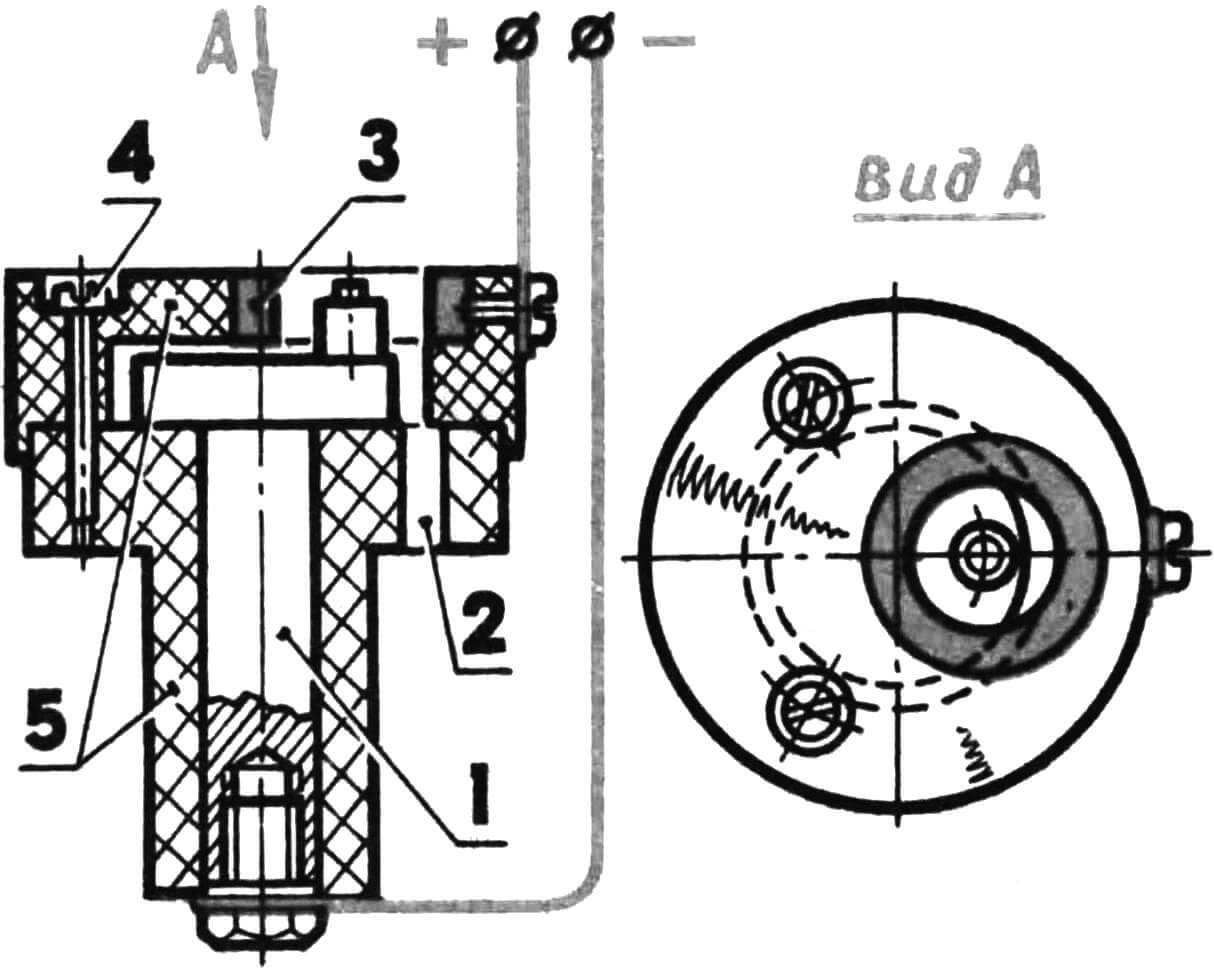
1 – колінвал (він же катод), 2 – наскрізне вікно для проходу електроліту, 3 – анод, 4 – гвинт кріплення кришки, 5 – деталі оправлення (фторопласт).
Після хромування всі вироби піддають термообробці протягом 2-3 годин для видалення водню при температурі 150-170°. Усі роботи ведуться під витяжним пристосуванням, у гумових рукавичках та окулярах.
ДЕФЕКТИ ХРОМУВАННЯ ТА ЇХ ПРИЧИНИ
1. Хром не осідає на виріб:
– поганий контакт у анода або катода,
– мало перетин провідників,
– на поверхні анода утворилася товста плівка оксидів (видаляється в розчині соляної кислоти),
– мала щільність струму,
– Висока температура електроліту,
– мала відстань між електродами,
– Надлишок сірчаної кислоти.
2. Покриття відшаровується:
– Погане знежирення поверхні,
– Порушувалася подача струму,
– Коливання температури або щільності струму.
3. На поверхні хрому – кратери, отвори:
– на поверхні деталі затримується водень – змінити підвіску так, щоб газ вільно видалявся,
– на поверхні основного металу є графіт,
– Поверхня основного металу окислена, пориста.
4. На виступаючих частинах потовщене покриття:
– Підвищена щільність струму.
5. Покриття жорстке, відшаровується:
– мала щільність струму, підвищена температура електроліту,
– у процесі хромування змінювалася температура електроліту,
— у процесі шліфування виріб перегрівся.
6. Хром не осідає навколо отворів деталі:
– велике виділення водню – закрити отвори пробками з ебоніту,
– Надлишок сірчаної кислоти.
7. На покритті коричневі плями: – Нестача сірчаної кислоти, – Надлишок тривалентного хрому (більше 10 г / л) – Витримати ванну під струмом без деталей, збільшивши поверхню анодів і зменшивши – катодів.
8. М’яке «молочне» покриття: – Висока температура електроліту, – Мала щільність струму.
9. Покриття матове, нерівне, важко притирається:
– Нестача хромового ангідриду – Велика щільність струму, – Нестача сірчаної кислоти, – Надлишок тривалентного хрому.
10. Покриття плямисте та матове: – в процесі хромування переривалася подача струму,
– Виріб перед завантаженням був холодний.
11. В одних місцях покриття блискуче, в інших матове:
– Велика щільність струму,
– Низька температура електроліту, – неоднакова щільність струму на виступаючих і поглиблених частинах деталі.
Ю. МУССАЛІТІН, майстер спорту СРСР