Для крышки (столешницы) гладильного столика подобрал лист многослойной 12-мм фанеры размерами 900×400 мм. Но можно использовать и панель из ДСП или (что еще лучше) мебельный щит из реек (досок) толщиной 15—20 мм. Оттолкнувшись от размеров выбранного фанерного листа, ориентируясь на приемлемую высоту установки рабочей поверхности (около 700 мм), выбрал и длину ножек.
Ножки столика сделал по типу промышленных — перекрещивающимися из двух фигурных дуг. Для дуг использовал дюралюминиевые трубки каркаса упомянутой старой раскладушки. Но таких трубок в каркасе без отверстий под пружины всего четыре. Чтобы не перегибать трубки, ножки пришлось делать составными, каждую из четырех Г-образных частей. Для этого распилил трубки каркаса так, как показано на рисунках.
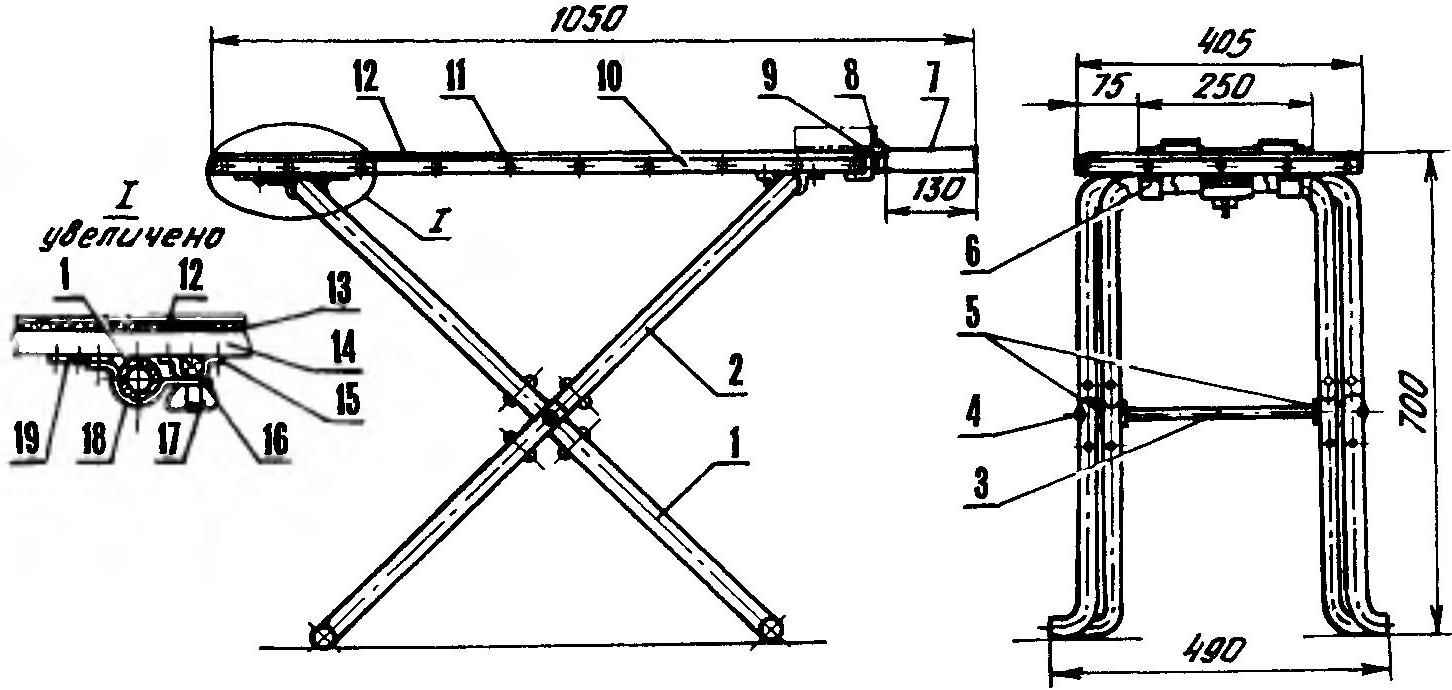
Столик для глажения:
1 —внутренняя ножка (дюралюминиевая труба 22×1,5 от раскладушки); 2—внешняя ножка (дюралюминиевая труба 22×1,5); 3 — распорная втулка (стальная труба); 4 — ось (сталь, круг d5); 5 — шайбы (капрон, лист s2, 4 шт.); 6 — скоба (СтЗ, полоса 30×2, 2 шт.); 7 — подставка под утюг (дюралюминиевый уголок 20×20, гетинакс s2); 8— карточная петля (2 шт.); 9 — кронштейн (выгнутый уголок 20×20, полоса 40×2); 10—кромочная полоса (пластик, полоса 10×2); 11 — гвоздь с декоративной головкой (30 шт.); 12 — чехол (плотная х/б ткань); 13 — ватин; 14 — панель столешницы (фанера s 12); 15 — обойма (СтЗ, полоса 40×2); 16— болт М10 с обточенной под квадрат головкой; 17 — барашковая гайка М10; 18 — скоба (СтЗ, полоса 40×2); 19 точная петля
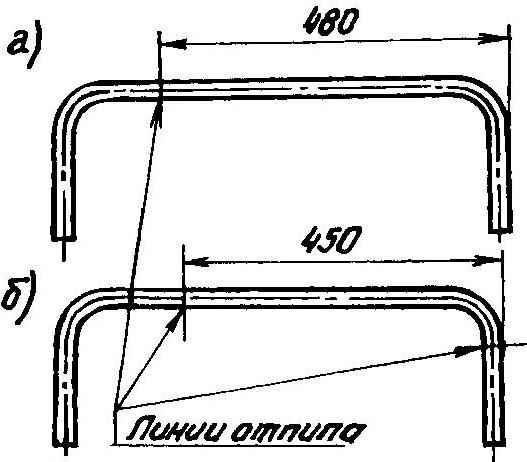
Раскрой трубчатых дуг раскладушки:
а — для верхней части ножек столика; б — для нижней части ножек столика
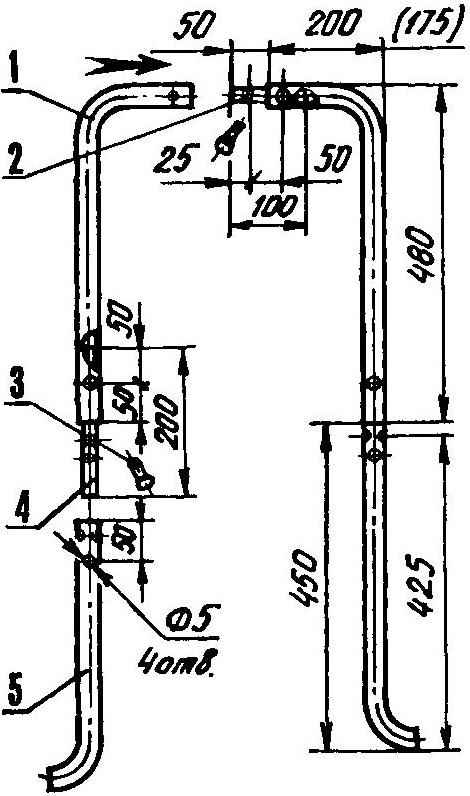
Сборка внешней (внутренней) ножки столика:
1 — верхняя полудуга ножки (2 шт.); 2 — верхняя соединительная втулка; 3 — дюралюминиевая заклепка (d5, 6 шт.); 4 — боковая соединительная втулка; 5 — нижняя часть ножки (2 шт.); детали 1,5 сделаны из дюралюминиевой трубы 19×1 от раскладушки; детали 2,4 — из стальной тонкостенной трубы 19×1
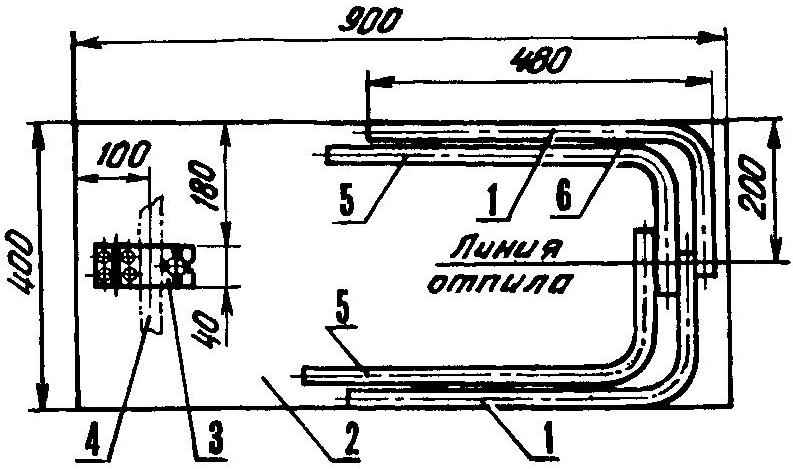
Схема укладки полудуг ножек иа нижней стороне панели столешницы для совместного отпиливання концов:
1 —полудуги наружной ножки (4 шт.); 2—панель столешницы; 3 — замок; 4 — внутренняя ножка; 5 — полудуги внутренней ножки (2 шт.); 6 — шайба (лист s2, 4 шт.)
Состыковал части при помощи стальных трубчатых втулок и алюминиевых заклепок от той же раскладушки по той же технологии, что и при изготовлении тележки.
Обе ножки соединил в месте перекрещивания осью из стальной проволоки. Чтобы ножки не сходились, на ось надел распорную втулку из тонкостенной стальной трубки. Выходящие наружу концы оси расклепал. Крепление наружной ножки к нижней стороне рабочей панели произвел двумя скобами с помощью шурупов. Скобы выгнул по полуокружности трубки из стальной полосы сечением 30×2 мм. Хомуты раздвинул к краям панели, но так, чтобы они не находили на изгиб трубки. Крепление внутренней ножки к панели — с помощью только одного хомута, но более широкого, откидного. Поэтому один его конец присоединил к одной карте шарнирной петли, а другую карту прикрутил шурупами к панели. На другом откидывающемся конце хомута вырезал паз под болт. Чтобы болт в обойме не проворачивался, его головку обточил под квадрат и заключил в обойму, которую прикрепил так же, как петлю, к низу панели. Для сборки столика приставил дугу ножки к панели, накрыл ее хомутом и его конец прикрутил барашковой гайкой к скобе головки болта.
На нижние концы ножек, чтобы они не царапали пол, надел подходящие пластмассовые пробки от бутылок.
И еще один узел—подставка под утюг. Ее каркас из дюралюминиевого уголка 20×20 мм, а дно — из листа гетинакса. Подставку сделал складывающейся, поэтому к торцу стола прикрепил ее с помощью двух карточных петель через кронштейн — выгнутый из стального листа уголок.
На рабочую (наружную) поверхность крышки столика положил слой ватина и закрыл его плотной хлопчатобумажной тканью. Края ткани подогнул и прикрепил к кромкам полосой пластика 10×2 мм и гвоздиками с декоративными шляпками.
В сложенном состоянии концы ножек немного выходят за кромки гладильного столика. Казалось бы, что этого не следовало делать. Но на практике получается только выигрыш. В рабочем положении у столика очень хорошая устойчивость, а при хранении в сложенном виде при установке столика «на ребро» он опирается на пол теперь не покрытой тканью доской, а концами ножек.
В.МАРТЫНОВ, г. В и т е б с к, Беларусь
Рекомендуем почитать
ЗИЛ-111: ПЯТЬ В ОДНОМ
Шестьдесят лет назад в первом выпуске журнала «Юный моделист-конструктор» вышла статья Юрия Долматовского «Автомобиль ЗИЛ-111В», заложившая основу рубрик «Знаменитые автомобили» и...
СЛУШАЕМ… НЕИСПРАВНОСТИ
Поиск неисправности в электронном устройстве, пожалуй, наиболее трудоемкая часть наладки или ремонта. Обычно для этой цели используют авометры, а также генераторы звуковой и модулированной...