Когда я завершил работу конструктором, приятель Алексей предложил применить «освобожденную творческую мысль»: спроектировать и сделать ему слайдер. Услышав впервые это слово, я подумал, что это приспособление для демонстрации слайдов…
— Зачем тебе слайд-проектор в наше время? — спросил я его.
— Просветитесь в интернете, Анатолий Васильевич! — мягко посоветовал Алексей…
Оказывается — теперь этим словом называют, кроме прочего, приспособление для плавного перемещения по нему видеокамеры или фотоаппарата при создании красивых видео из энергичных проездов и таймлапсов (видео, созданное из серии фотографий, снятых неподвижной или плавно движущейся камерой в течение длительного промежутка времени)! По-русски это называется — операторские рельсы.
Просмотрев картинки и видео нескольких фирменных и самодельных слайдеров, понял суть их применения, вник отчасти и в конструкцию. Провел несколько телефонных консультаций со знакомыми кинооператорами про длину и ширину рельс; про плавность хода и размеры присоединительной резьбы.
Есть два типа слайдеров, вполне доступных для самостоятельного изготовления. Первый основан на передвижении каретки с камерой по гладким направляющим. Второй — каретку устанавливают на подшипниках и перекатывают по рельсам. Недостатки слайдеров на основе трения в том, что если аппаратура тяжелая, то и сопротивление передвижению немалое. При этом не исключены и рывки, что может испортить съемку. У слайдеров с каретками, установленными на подшипниках, такого не происходит — их движение плавное, практически без сопротивления. Правда, они сложнее по конструкции и значительно дороже.
Несмотря на это, решил все же создать слайдер второго типа, доступный в изготовлении своими силами и «демократичный» по цене. Начертил эскиз. Прорисовывая каретку на подшипниках, нашел ей оптимальную форму в виде угловатой буквы «С». В качестве основного материала решил использовать имевшийся в наличии листовой дюралюминий толщиной два-три и пять миллиметров.
Совершил поход по местным магазинам и приобрел большинство необходимых материалов: два отрезка никелированной тонкостенной трубы мебельной фурнитуры диаметром 25 мм и длиной по 750 мм, четыре торцевых пробки — мебельные подпятники ножек на резьбе М10 и шесть импортных подшипников с внутренним диаметром 7 мм и наружным — 22 мм.
Еще купил комплект болтов М5х25 с шайбами и гайками, пакет отрывных заклепок 4×8 мм и аэрозольный баллончик с акриловой черной матовой краской.
На следующее утро пошел в домашнюю мастерскую и принялся за дело. Из-за печки вытащил куски небольших листов дюралюминия различной толщины — запасы еще с советских времен, с местного военного завода.
Собрал и разложил на верстаке необходимый инструмент: штангенциркуль, металлическую линейку, угольник и чертилку. Разметил на листе дюралюминия развертки каретки, кронштейна и двух ножек. По хорошо видимым линиям вырезал дискорезом заготовки.
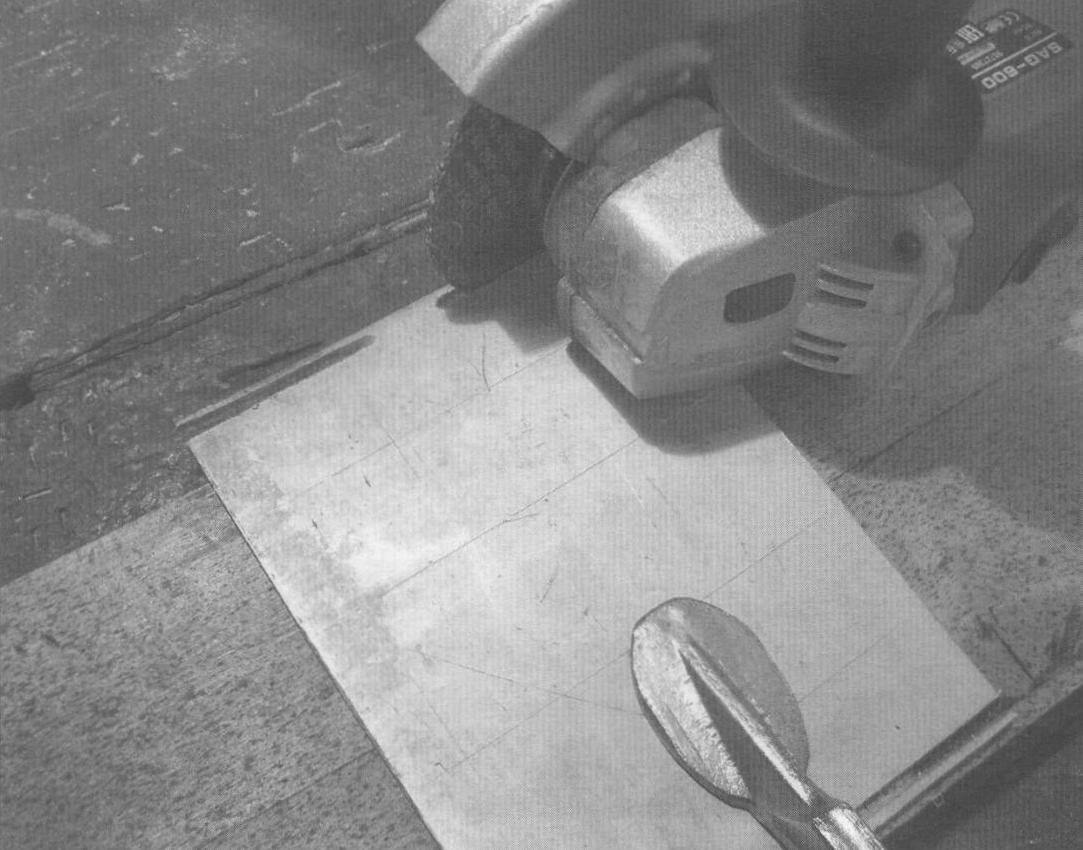
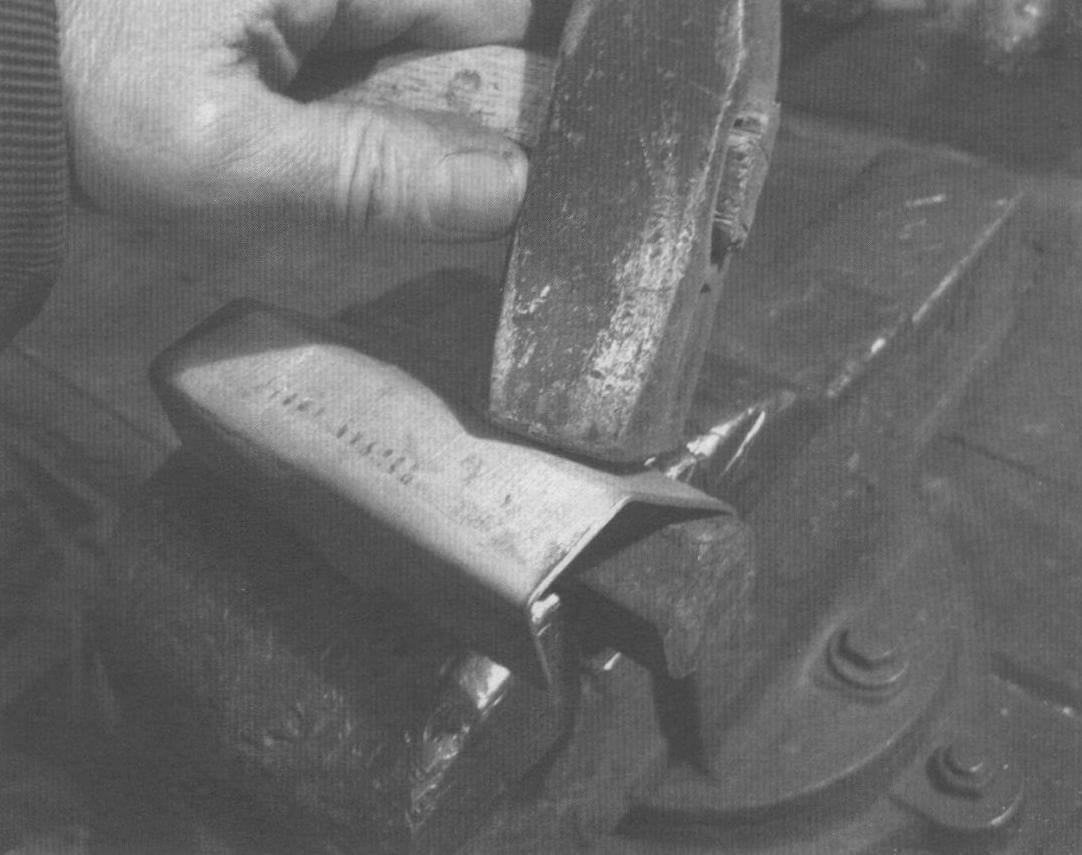
На стационарном наждаке обработал ребра, закруглил углы и зачистил заусенцы. Наждачной бумагой отполировал все поверхности и кромки. В больших слесарных тисках молотком по намеченным линиям произвел гибку заготовки каретки, кронштейна и двух ножек. После этого откорректировал размеры и отрихтовал детали согласно эскизам.
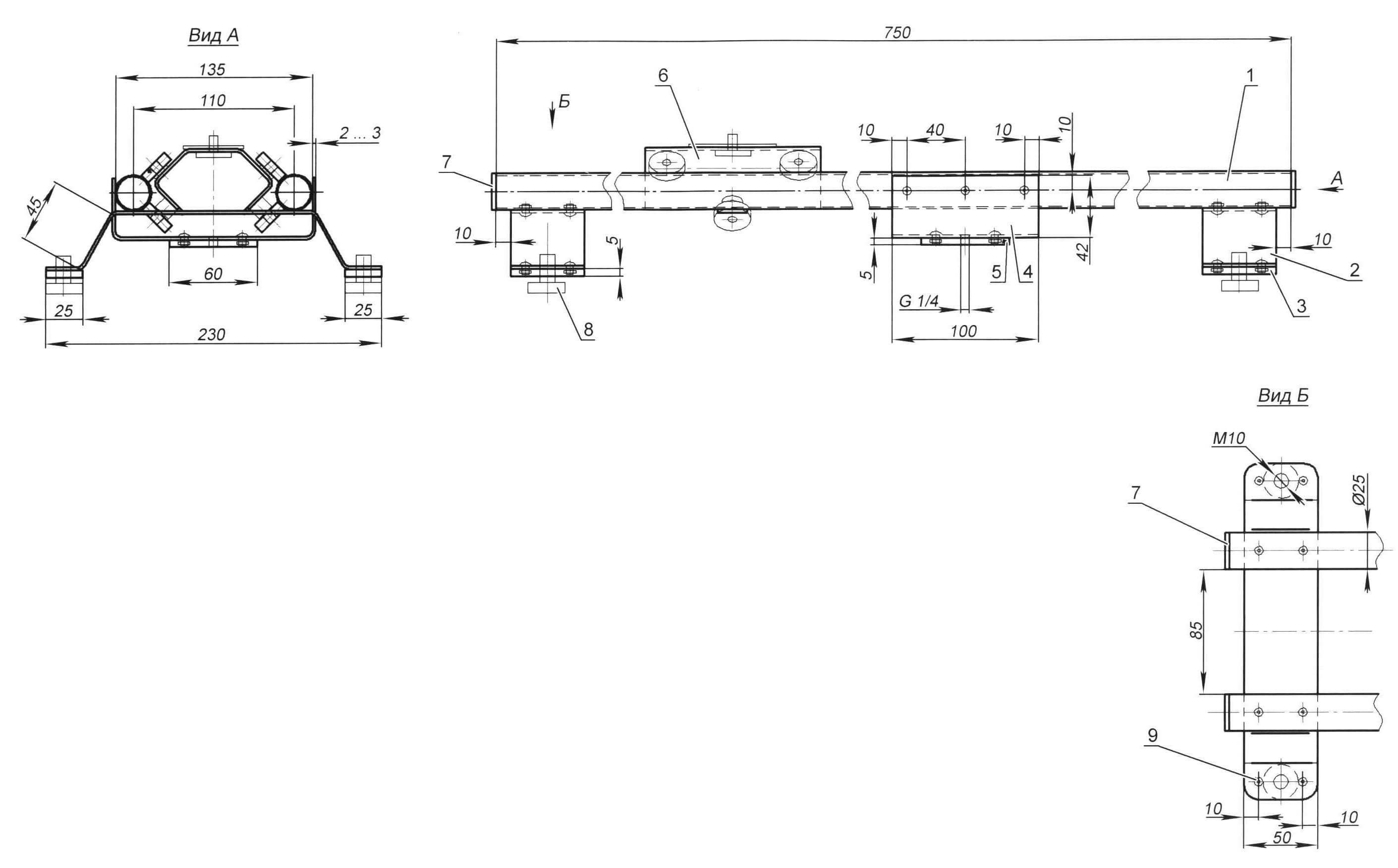
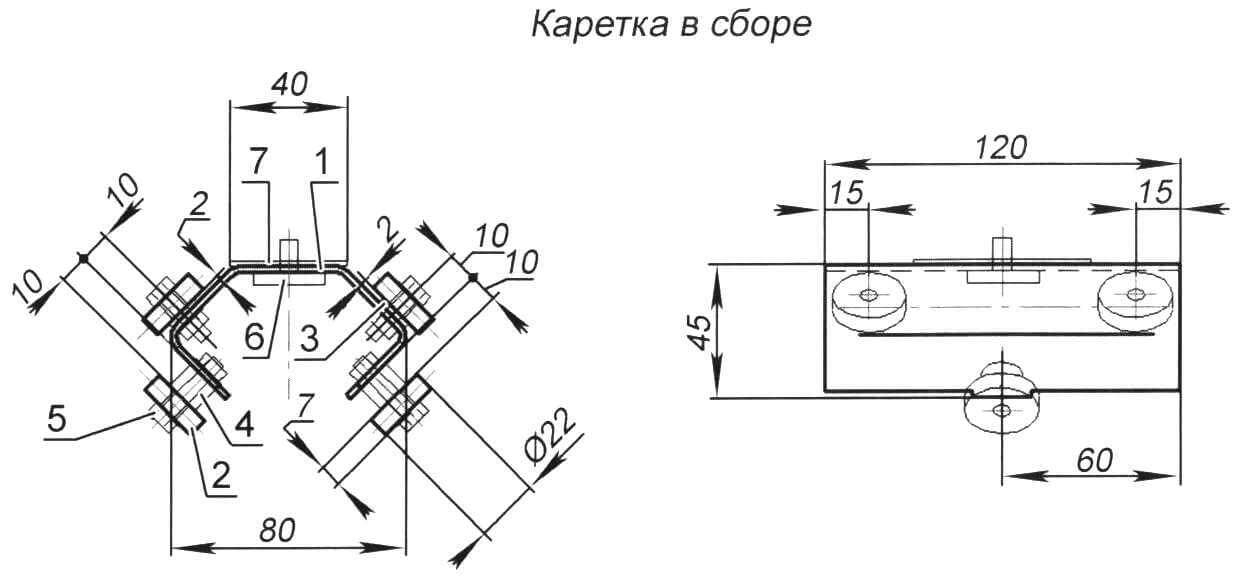
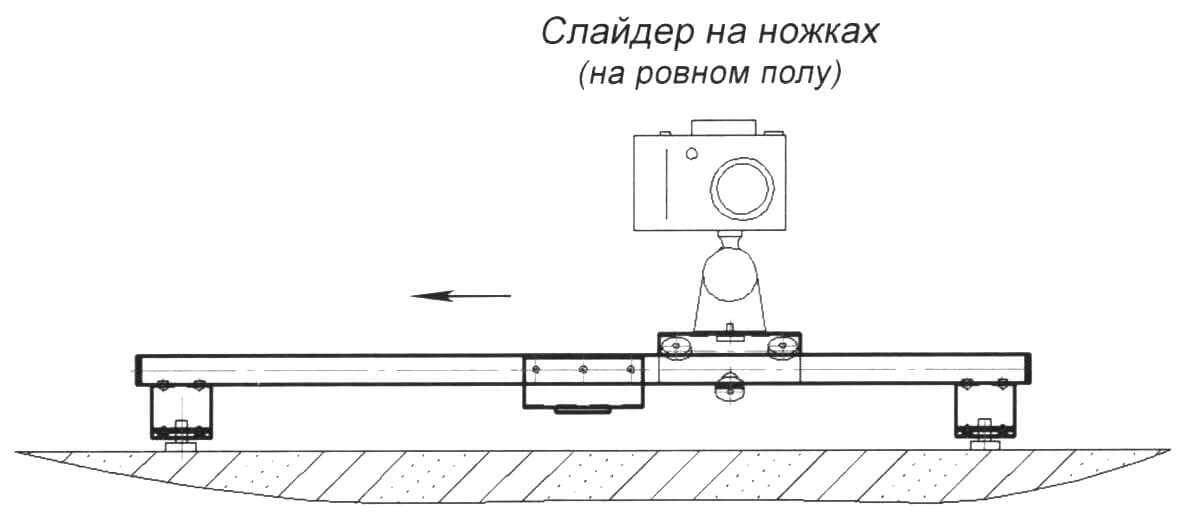
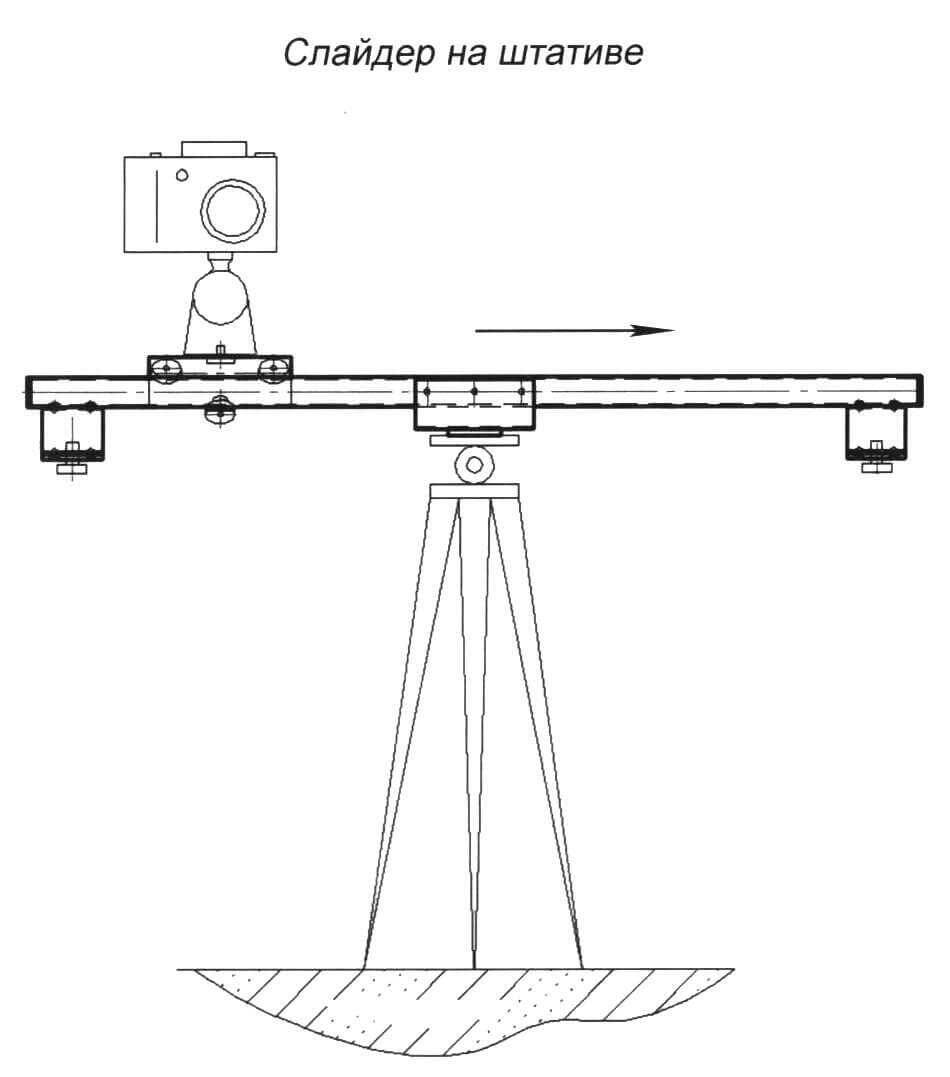
Следующий этап — разметка и сверление отверстий диаметром 5 мм в ножках, в кронштейне и в каретке, а также снятие с них заусенцев большим сверлом, проворачивая его рукой.
Для установки подшипников на корпус каретки потребовалось выточить на токарном станке из дюралюминиевого прутка диаметром 10 мм опорные втулки двух размеров. Всего их шесть штук. Четыре выточил по длине опор — 2 мм, посадочный диаметр — 7 мм и внутреннее отверстие — 4 мм. И последние две втулки — с такими же отверстиями, но длиной опоры 10 мм.
Сборку каретки произвел на метизы М5 и поставил ее на рельсы.
Межосевое расстояние в 110 мм обеспечил простейшим кондуктором из деревянных брусков с прижимом столярными струбцинами.
Проверка движения каретки на плавность прошла удачно.
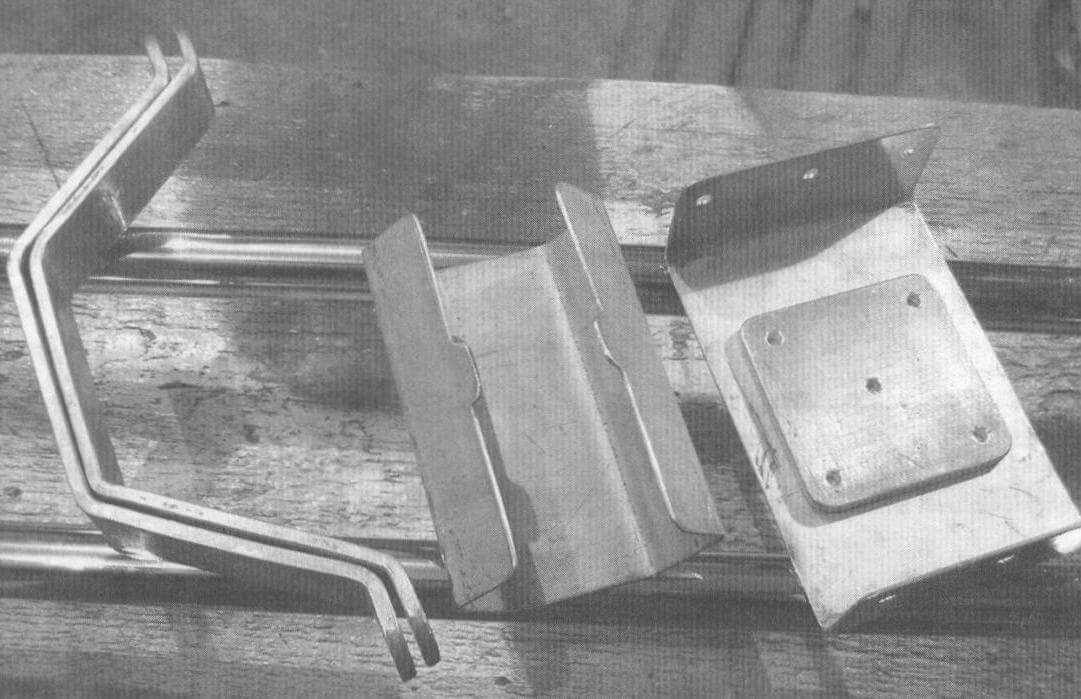
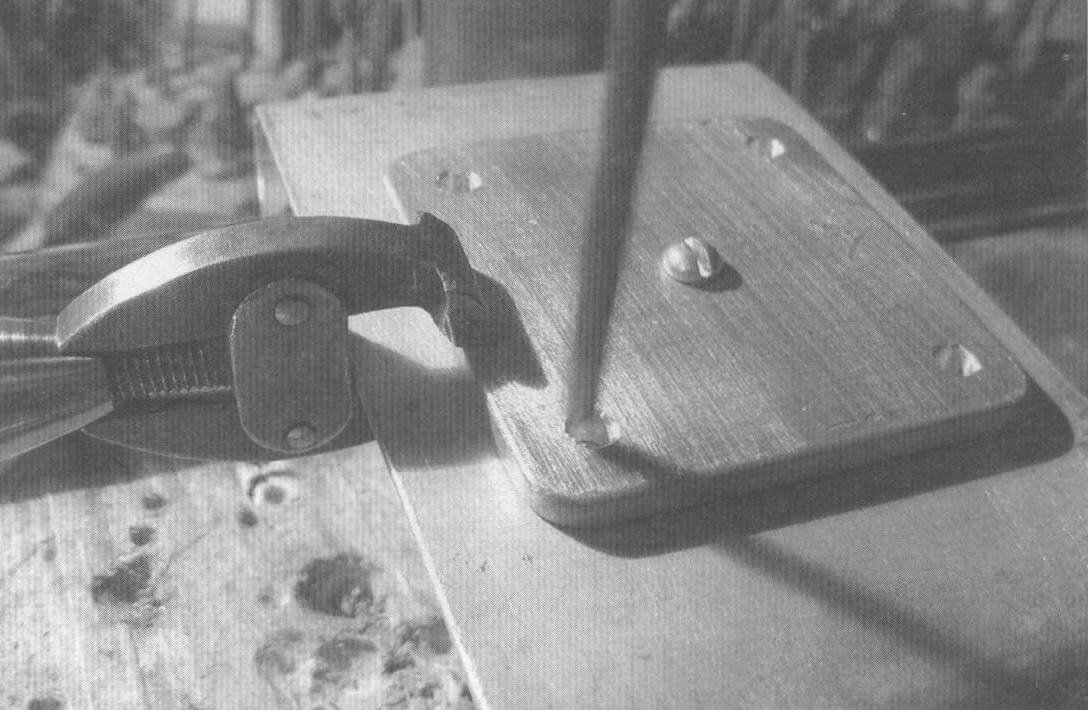
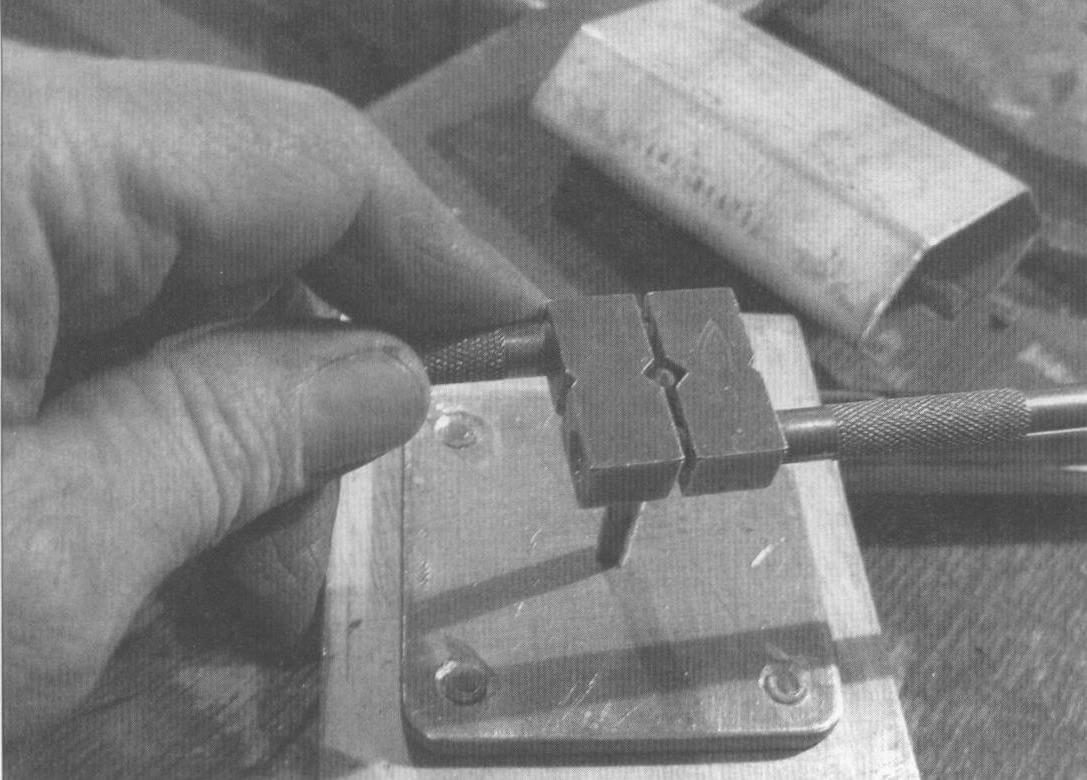

Разметил и поочередно просверлил крепежные отверстия в трубах. Ножки — левую и правую — прикрепил к рельсам двумя заклепками каждую. Центральный кронштейн — шестью отрывными заклепками.
Для увеличения длины присоединительной резьбы для штатива приклепал под кронштейн накладку из 5-мм алюминиевой пластины. Затем нарезал центральное резьбовое отверстие в ¼ дюйма (как на штатном винте).
С этой же целью из дюралюминиевой пластины такой же толщины приклепал накладки к ножкам. Затем нарезал в них резьбовые отверстия М10 и вкрутил мебельные ножки.
Еще в центре корпуса каретки разметил и просверлил отверстие диаметром 6 мм и установил штатный винт с резьбой ¼ дюйма от фотокамеры. Сверху надел резиновую накладную шайбу диаметром 50 мм.
Декоративные пробки установил в торцевые отверстия трубчатых рельсов — этим и завершил изготовление первого моего слайдера.
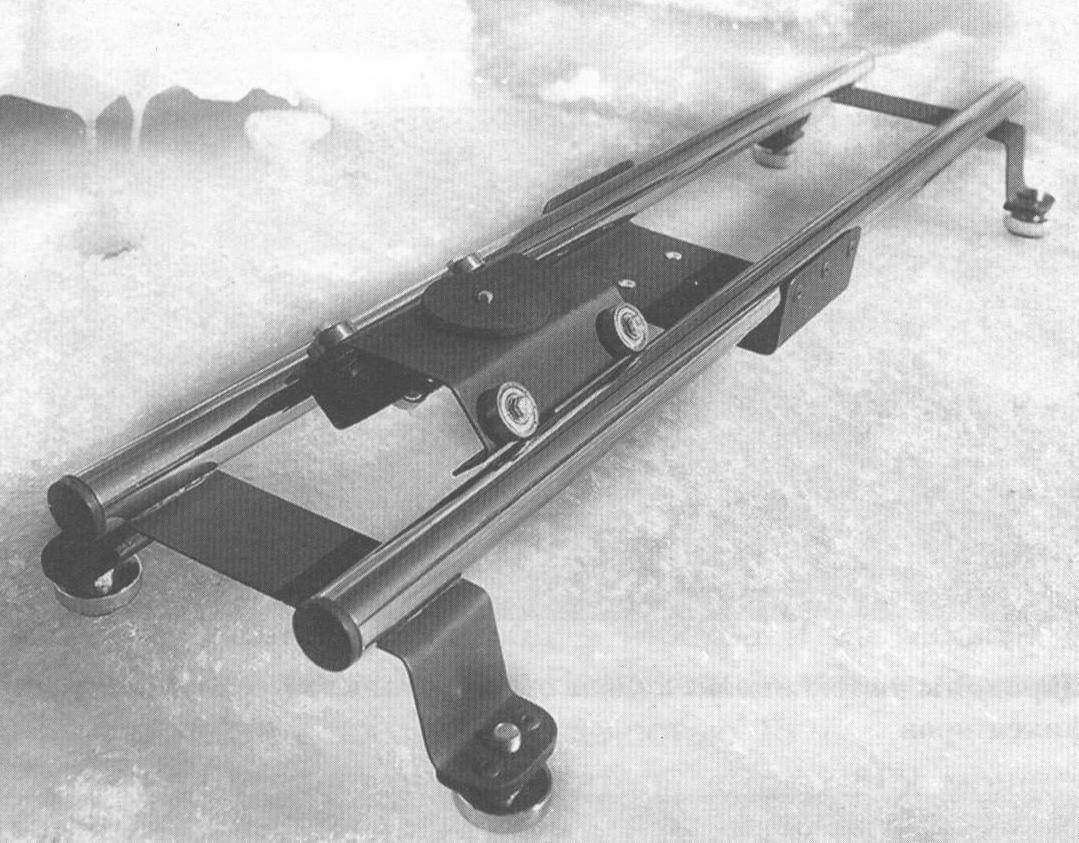
Скорость реализации идеи очень удивила приятеля Алексея. Ведь первое пробное изделие всегда предполагает проверку на деле идей, материалов и размеров. Опытный экземпляр делал не торопясь и дорабатывал все по месту.
Осмотр и испытания на плавность хода заказчиком подтвердили правильность примененных решений и нареканий не вызвали:
— Просто отлично! Ничего лишнего. Габариты, вес и прочность оптимальны!
— Ну, тогда и я сделаю себе такой же и буду учиться снимать клипы! — сообщил я приятелю.
Осталось только покрасить все дюралюминиевые детали черной матовой краской. Правда, пришлось слайдер частично разобрать и защитить малярным скотчем никелированные трубки.
НЕКОТОРЫЕ ОСОБЕННОСТИ КОНСТРУКЦИИ И СБОРКИ
Для корпуса каретки и ножек можно применить листовую оцинкованную сталь или «нержавейку», а трубы-рельсы — из полированного алюминия. При других подшипниках придется применить и другие втулки и болты. Отверстие для крепления нижнего подшипника должно быть овальным. Допустимы незначительные погрешности при разметке, сверлении и вырезании.
В следующим слайдере намерен удлинить рельсы, сделать съемные ножки, нарезать резьбу в крайних опорах для двух штативов, возможно даже установлю электропривод…
А. МАТВЕЙЧУК
г. Заводоуковск,
Тюменская обл.