Мотор работал на топливе, состоящем из смеси бензина АИ-93 (удельный вес 0,74) и масла МГД-14М в пропорции 1:30. Топливо самотеком поступало из расходного бака, установленного на высоте 2,5 м относительно карбюратора.
Перед испытаниями были проверены фазы газораспределения, уточнена эффективная степень сжатия — она составила величину Еэф = 5,6. Была отмечена низкая величина среднего эффективного давления серийного двигателя — всего 3,56 кг/см2.
Все операции, связанные со снятием характеристик, проводились на комплексном моторном стенде, изготовленном в авиационном отделе Научно-технического центра «Исток» и позволявшем одновременно регистрировать величины крутящего момента, расхода топлива, числа оборотов и температуры головок цилиндров.
Стенд включает в себя балансирный станок, мулинетку (деревянный воздушный винт диаметром 840 мм), расходомер топлива (штихпробер) с герметичными контактами (герконами), термопару со стрелочным индикатором и расходный топливный бак емкостью 10 л.
Для изменения момента сопротивления на концы лопастей мулинетки крепились шесть пар сменных тормозных пластин, что позволяло получить семь точек замеров параметров внешней характеристики.
Мерительная база штихпробера состояла из трех объемов, контролируемых герконами, магнитного поплавка и трехходовых кранов. Электронный тахометр — бесконтактный, с индукционным датчиком. Измеритель температуры — авиационный, регистрирующий температуру головок цилиндра под свечой.
Для уменьшения сил трения все подвижные соединения станка оснащены подшипниками качения.
Работы проводились в четыре этапа:
1) снятие исходных (контрольных) характеристик серийного двигателя;
2) модернизация;
3) снятие характеристик модернизированного двигателя и проверочный облет его на дельталете;
4) снятие характеристик модернизированного двигателя без воздуходувки и редуктора.
Первый этап осуществлялся на комплексном моторном стенде.
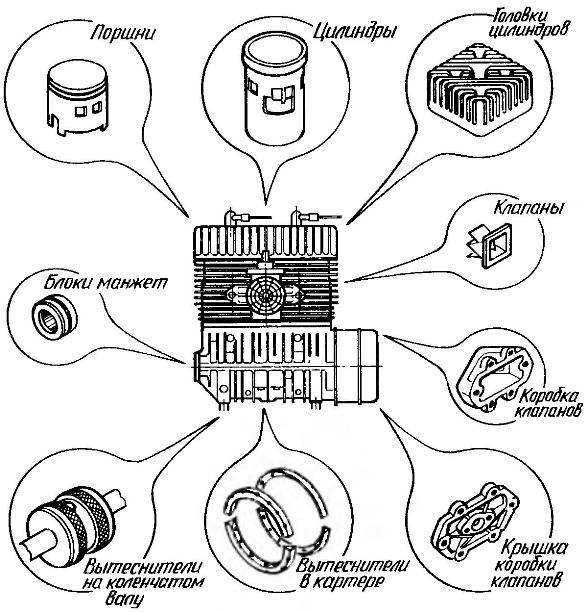
Рис. 1. Узлы и детали серийного двигателя РМЗ-640 «Буран», которые были вновь изготовлены или модернизированы.
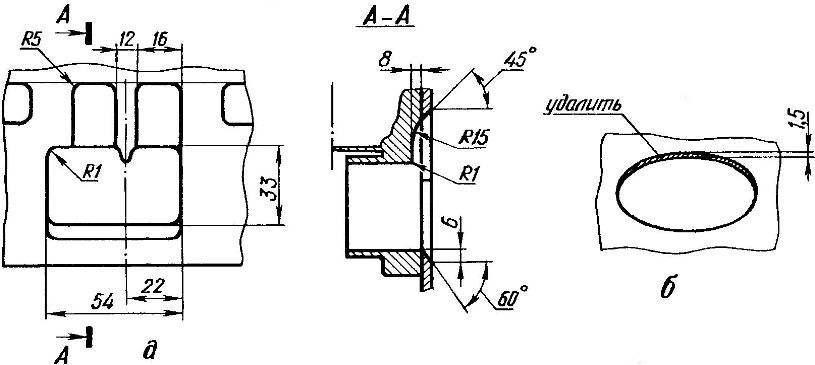
Рис. 2. Доработанные впускное (а) и выпускное (б) окна цилиндра (поверхность цилиндра развернута в плоскости чертежа).
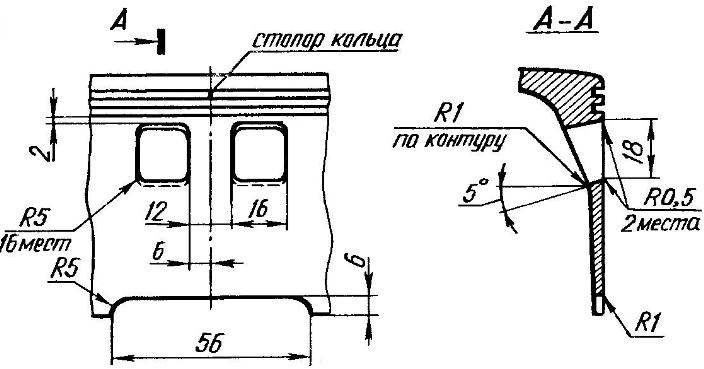
Рис. 3. Доработанный поршень (поверхность поршня развернута в плоскости чертежа).
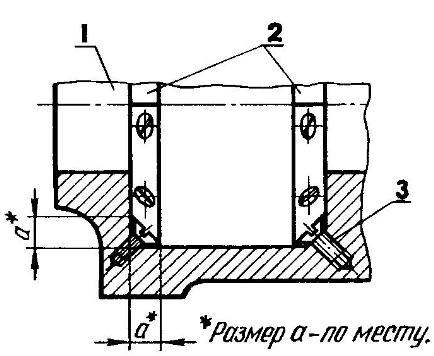
Рис. 4. Вытеснители в картере:
1 — камера кривошипная; 2 — вытеснители (АМг-6); 3 — винт М4 (20 шт.).
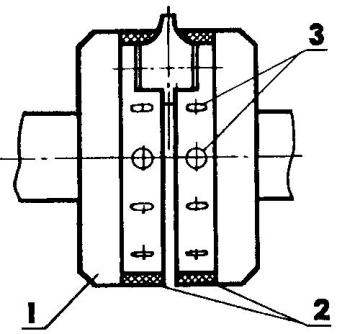
Рис. 5. Вытеснители на коленчатом валу:
1 — коленвал; 2 — вытеснители (стеклонить на эпоксидном связующем); 3 — лунки (сверление d4 на глубину 0,5 мм, 20 шт.).
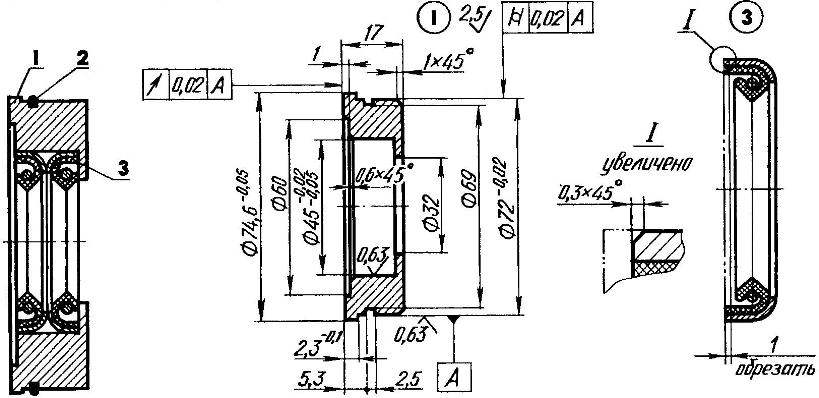
Рис. 6. Блок манжет:
1 — обойма (анодированный Д16Т); 2 — кольцо уплотнительное, резиновое (от ВАЗ-2108); 3 — манжета (от ВАЗ-2101, обрезанная).
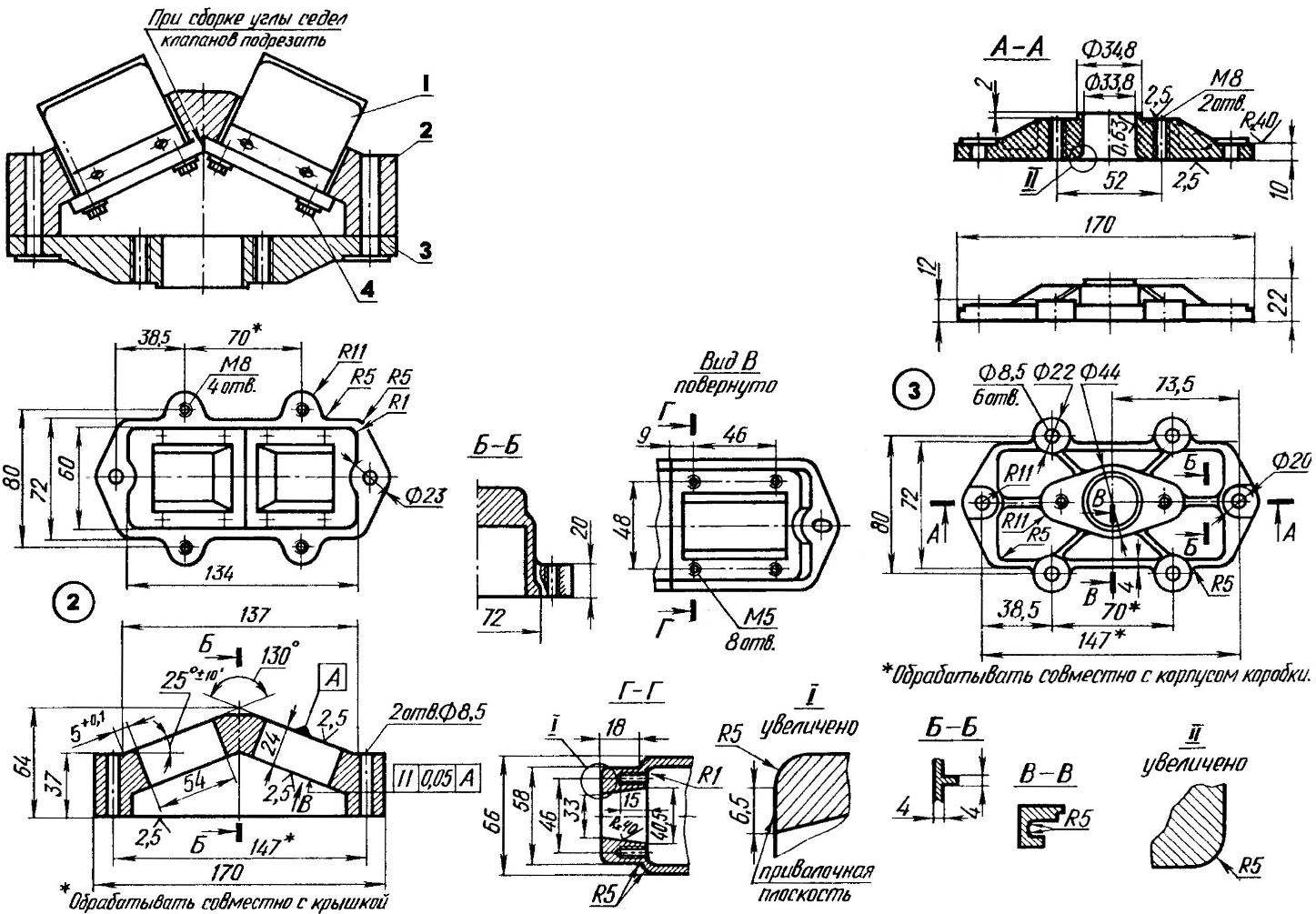
Рис. 7. Коробка клапанов:
1 — клапан пластинчатый (2 шт.); 2 — корпус коробки (АЛ1); 3 — крышка (АЛ1); 4 — винт М5 (8 шт.).
Условия испытаний: температура наружного воздуха +2°С; атмосферное давление — 746 мм рт.ст.; топливо — смесь бензина АИ-93 с маслом МГД-14М (1:30); карбюратор — К-62Ж (диаметр главного жиклера — 1,36 мм; эффективная степень сжатия Еэф = 5,6); свечи — А17ДВ.
Были получены следующие результаты.
Винтовая характеристика (внешняя нагрузка — воздушный винт диаметром
1,6 м и шагом 0,79 м): Ne = 25,8 л.с. при 5086 об/мин, Се = 0,433 кг/ч л.с.
Внешняя характеристика (внешняя нагрузка — мулинетка): Ne = 27,9 л.с. при 5514 об/мин, Се = 0,416 кг/ч л.с. Температура головки t°C = 212°С.
Второй этап — собственно модернизация. Доработке подверглись; картер (в углах кривошипной камеры установлены вытеснители), головки цилиндров (опорные поверхности головок подрезаны на
1,8 мм для увеличения эффективной степени сжатия, Еэф повысилась до 7,2, сами цилиндры (расточены впускные и выпускные окна), коленчатый вал (в выемках щек установлены вытеснители), манжеты коренных шеек коленвала (обрезаны на 1 мм). Расточен также диффузор карбюратора до диаметра 33,6 мм, увеличен диаметр главного жиклера до 2,12 мм, уменьшена высота распылителя на 0,76 мм.
Фазы газораспределения (впуска и выпуска) увеличены. В каждом цилиндре изготовлены два дополнительных канала перепуска с фазами, равными фазам основных каналов (гильза цилиндра при этом не выпрессовывалась).
Изготовлены заново; поршни, коробка клапанов, крышка коробки, обратные пластинчатые клапаны (пластины, седла и ограничители), обоймы манжет.
Поршни откованы из сплава АК12Д. Они имеют по два продувочных окна, что снизило температуру верхних колец и головок поршней и исключило их прогар.
В отличие от серийного, юбка нового поршня имеет бочкообразность и эллипсность в соответствии с температурным градиентом. Геометрия юбки доводилась экспериментально. Поскольку процесс этот довольно сложный, то можно оставить и штатные поршни, доработав их по прилагаемым чертежам.
Корпус и крышка коробки обратных пластинчатых клапанов отлиты из АЛ1. Однако возможно применение любого другого литейного термообрабатываемого алюминиевого сплава.
Седла клапанов изготовлены прессованием из органита (или кевлара, как еще называют этот СВМ — сверхвысокопрочный материал) на эпоксидном связующем с подогревом до 80—85°С в процессе полимеризации. Размеры седел с небольшими изменениями взяты из книги В.М.Кондрашева и других (см. Литература). Материал пластин клапанов — стеклотекстолит СТЭФ-1, ограничителей — сталь.