Машину эту я начал конструировать давно — может быть, десять, может, пятнадцать лет назад. Но это вовсе не означает, что все десять-пятнадцать лет я простоял за кульманом. Нет, просто по крупицам в массе уже созданного и отработанного выискивал «золотые самородки» тех единственных конструкторских решений, которые легко укладывались в уже сложившуюся для меня концепцию городского автомобиля и наиболее эффективные и простые технологические приемы. Ну и, конечно, привнес в эту конструкцию и несколько своих идей — ведь под «чужие» никогда не найдешь в себе ни истинно творческих сил, ни конструкторской находчивости, ни технологической изворотливости.
Конечно, поначалу требования мои к будущей машине были явно чрезмерными — это относилось и к габаритам, и к мощности и, соответственно, к будущим затратам. Но с течением времени техническое задание, сократившись буквально до нескольких строк, стало выглядеть приблизительно так:
«Машина должна быть чрезвычайно простой, чтобы ее можно было построить, не прибегая к сложному станочному оборудованию; возможно более легкой с тем, чтобы при двигателе сравнительно небольшой мощности она обладала хорошими динамическими характеристиками; иметь минимальные внешние габариты; обеспечивать удовлетворительный комфорт водителю и его единственному пассажиру; наконец, машина обязательно должна быть недорогой в «домашнем производстве» и иметь привлекательный внешний вид».
Вот, собственно, и все требования. Исходя из них, постепенно и создавался облик этого компактного и простого двухместного городского автомобиля, получившего впоследствии название «АРБАТ».
***
ВЫБОР ДВИГАТЕЛЯ. С удовольствием поставил бы на свой автомобиль небольшой экономичный четырехтактный двигатель мощностью около двадцати сил, однако таких промышленность пока не выпускает. Пришлось довольствоваться мотором от «Тулицы» рабочим объемом 200 см3 и мощностью 14 л. с. Тем не менее впоследствии я ни разу не пожалел о выборе. Простой, малошумный, достаточно мощный, надежный, да к тому же еще и оснащенный стартером движок — чего еще можно желать для самоделки!
ВЫБОР СХЕМЫ ПЕРЕДАЧИ. Крутящий момент от двигателя к задним колесам передается обычно у всех машин через дифференциал. С самого начала я решил отказаться от этого тяжелого и громоздкого механизма, а чтобы при поворотах не «жевало» резину покрышек — соединить колеса с двигателем через обгонные муфты. Правда, при этом автомобиль лишался заднего хода и возможности тормозить двигателем. Однако для сверхлегкого городского автомобиля, эксплуатируемого преимущественно в весенне-летне-осенний период, это не столь уж и важно.
Конструктивно передача планировалась двухступенчатой. От двигателя момент вращения должен передаваться цепью на промежуточную центральную звездочку, закрепленную на двухсторонней роликовой обгонной муфте, а та — приводить во вращение полуоси. На концах полуосей — еще две промежуточные звездочки, которые втулочнороликовыми цепями соединяются со звездочками задних колес.
ВЫБОР СХЕМЫ КУЗОВА И РАМЫ. Задача эта оказалась для меня особенно сложной. Поначалу планировал сварить плоскую — как у карта — раму и установить на нее выклеенный по болванке из стеклоткани и эпоксидной смолы кузов. Но такая конструкция получалась неоправданно трудоемкой, сложной, тяжелой, да и не слишком прочной.
Дело не сдвигалось с места, пока мне не пришло в голову в качестве жесткой основы кузова-каркаса воспользоваться двумя старыми дверями от автомобиля ВАЗ-2105. Использование в качестве несущих элементов дверей автомобиля помогло и при прорисовке внешнего вида кузова машины — заложило основу ее дизайна.
Две двери, соединенные поперечными элементами, образуют жесткую коробку — основу кузова. Правда, на моем автомобиле эти двери своей изначальной функции не выполняют: ни правая, ни левая не открываются, а водитель и пассажир пользуются единственной настоящей дверью — задней. Как оказалось, для молодежного автомобиля такая компоновка не только вполне допустима, но и имеет свое достоинство: задняя дверь не уменьшает жесткости кузова, и, таким образом, можно существенно уменьшить массу автомобиля за счет отказа от двух массивных и прочных дверных коробов. Откидывается задняя дверь вверх — как у большинства современных автомобилей с кузовом типа «хатчбэк». Расстояние между сиденьями позволяет проходить и на водительское, и на пассажирское места. К тому же каждое из кресел имеет шарнирную спинку, которая складывается вперед и откидывается к боковой панели.
ВЫБОР ТЕХНОЛОГИИ ИЗГОТОВЛЕНИЯ КУЗОВА. Для домашних условий наиболее приемлемы выклейка корпуса в матрице или по болвану. Однако оба способа требуют сложной технологической оснастки, сделать которую подчас труднее, чем собственно выклейку. Размышления и эксперименты позволили мне разработать эффективный безматричный способ выклейки стеклопластиковых панелей двойной кривизны.
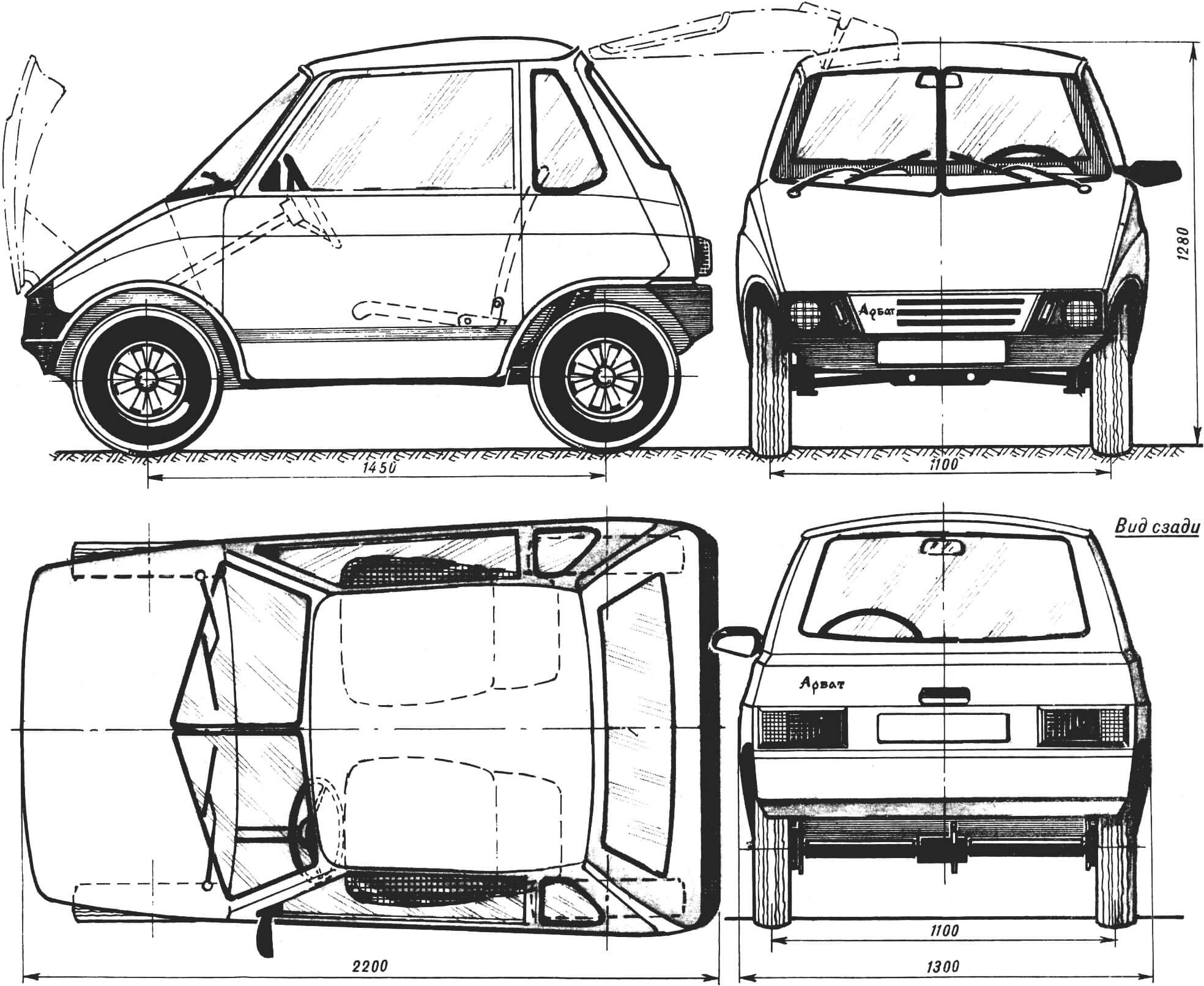
Теперь подробнее и по порядку о том, как сделать в условиях самой примитивной мастерской автомобиль, подобный моему «Арбату». Как показали многочисленные прорисовки, для кузова вполне подойдут двери практически любого легкового автомобиля — в частности, широкие двери «Запорожцев» любой модели. Мне же, как уже упоминалось, достались бывшие в употреблении двери «Жигуленка» ВАЗ-2105.
Для начала обе двери я тщательно выставил на ровном полу и временно соединил друг с другом так, как они окажутся на будущем автомобиле. Причем взаимная ориентация их, разумеется, была совсем не той, что на ВАЗ-2105: на «Арбате» они имеют больший наклон к плоскости пола (внутрь).
Далее заготовил три тонкостенных (1,5 мм) трубы с внешним Ø 50 мм и подогнал их к нижним частям дверей, одну спереди и две сзади: трубы составили основу рамы. А еще две трубы Ø 30 мм, соединившие верхние части дверей, замкнули конструкцию — получилась жесткая коробка-салон.
Теперь — очередь подвески. У «Арбата» задние колеса подвешены на продольно качающихся рычагах, подрессоренных с помощью амортизаторов мотоцикла «Иж-Планета» или «Иж-Юпитер». Каждый из рычагов подвески шарнирно закреплен в кронштейнах, вырезанных из пятимиллиметрового стального листа и приваренных к двум задним трубам коробки-салона. Качание — во фторопластовых или бронзовых втулках-вкладышах, закрепленных на кронштейнах.
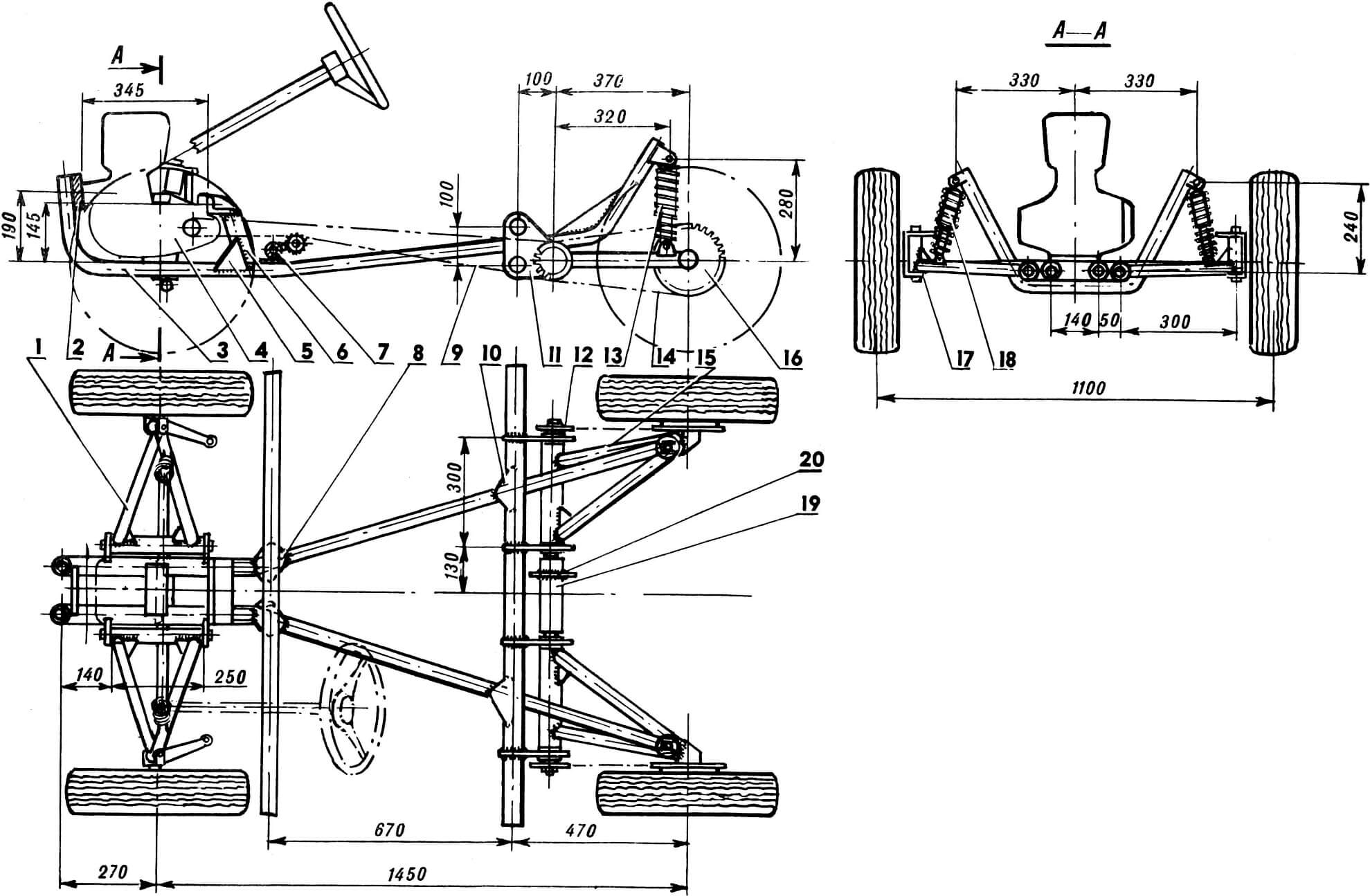
1 — рычаг передней подвески, 2 — передний узел крепления двигателя, 3 — продольный лонжерон рамы, 4 — двигатель Т-200, 5 — усиливающая косынка, 6 — задний кронштейн крепления двигателя, 7 — передняя поперечина рамы, 8 — усиливающая косынка, 9 — втулочно-роликовая цепь первой ступени, 10 — усиливающая косынка, 11 — кронштейн, 12 — боковая промежуточная звездочка, 13 — амортизатор, 14 — цепь, 15 — рычаг задней подвески, 16 — звездочка заднего колеса, 17 — поворотная вилка, 18 — амортизатор передней подвески, 19 — обгонная муфта, 20 — центральная промежуточная звездочка.
Чтобы избежать рывков в трансмиссии, промежуточные валы и ось качания задних колес совмещены: внутри каждого из трубчатых поперечных элементов задней подвески проходят промежуточные валы, вращающиеся в подшипниках №204. С внешней стороны каждого из валов винтовыми шпонками закреплена звездочка, с внутренней валы объединены двухсторонней роликовой обгонной муфтой.
Сама обгонная муфта представляет собой стальную втулку с приваренной к ней звездочкой. Ответная часть муфты — это внутренние части промежуточных валов, на которых профрезерованы уступы и просверлены глухие отверстия под пружины.
Попутный технологический совет: чтобы промежуточные валы располагались строго соосно, кронштейны подвески лучше всего приваривать, посадив их на трубу соответствующего диаметра.
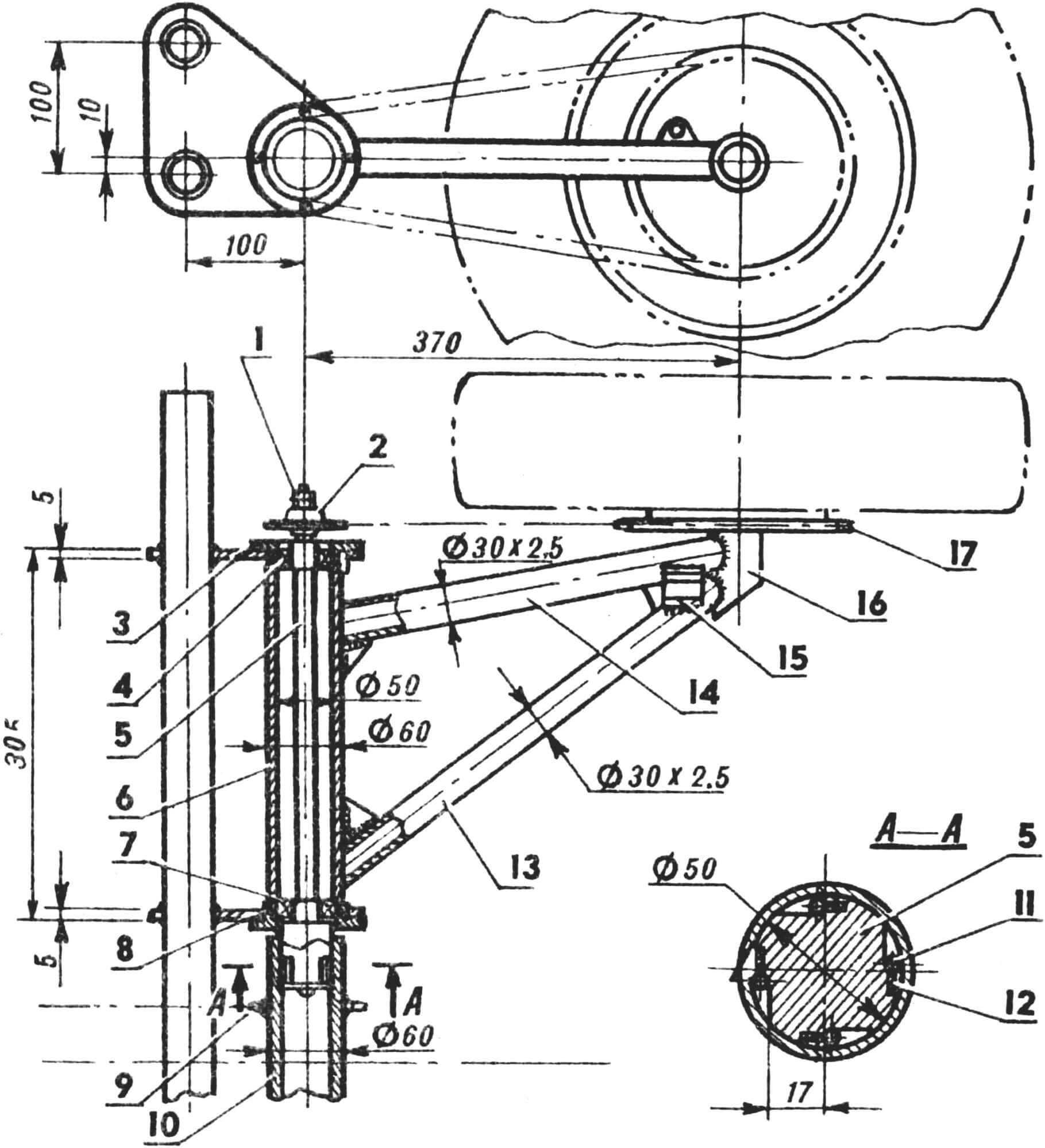
1 — гайка и контргайка крепления промежуточной звездочки, 2 — промежуточная звездочка, 3 — подшипник скольжения рычага подвески, 4 — подшипник шариковый (№ 205), 5 — вал промежуточной звездочки, 6 — корпус рычага, 7 — подшипник шариковый (№ 205), 8 — подшипник скольжения, 9 — промежуточная центральная звездочка, 10 — корпус обгонной муфты, 11 — ролик обгонной муфты, 12 — пружина, 13 — внутренняя труба рычага подвески, 14 — внешняя труба рычага подвески, 15 — кронштейн-вилка амортизатора подвески, 16 — ось, 17 — ведомая звездочка.
Рычаги задней подвески сварены из двух отрезков труб Ø 30X2 мм и трубы Ø 52X4 мм. Ось заднего колеса вытачивается по образцу и подобию оси мотороллера «Турист» или «Тулица».
Продольные лонжероны рамы согнуты с помощью трубогиба с предварительной набивкой труб просеянным песком. К поперечным балкам они привариваются с использованием усиливающих косынок из стального листа толщиной 2 мм. Задние и передний узлы под крепление двигателя желательно устанавливать «по месту» — с предварительной подгонкой кронштейнов, фиксацией их на двигателе, прихваткой несколькими точками сварки и после снятия двигателя — окончательной приваркой пластин и кронштейнов. Точно так же следует приваривать вилки, в которых устанавливаются амортизаторы задней подвески.
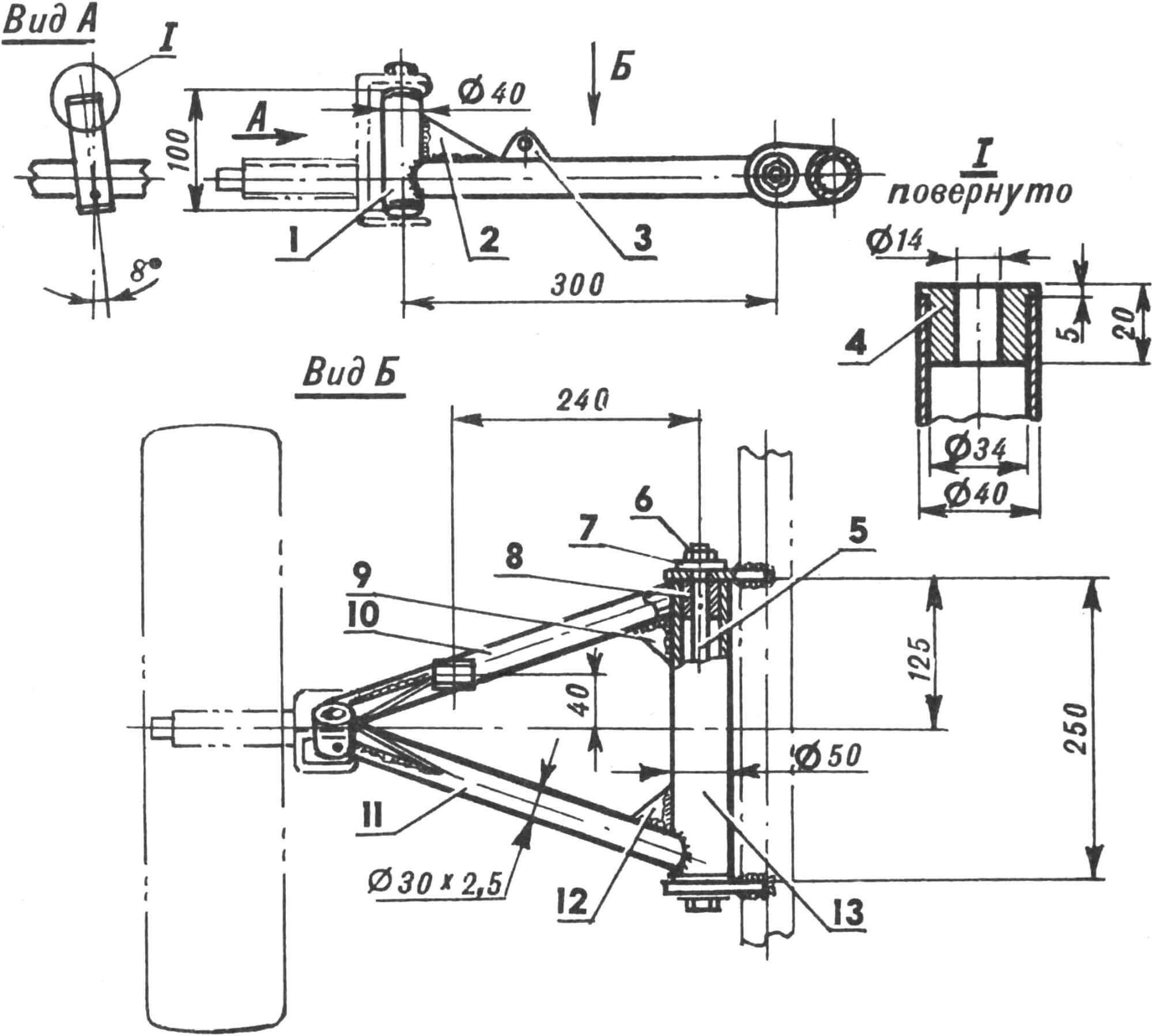
1 — шарнир поворотной вилки колеса, 2 — косынка, 3 — кронштейн-вилка амортизатора подвески, 4 — бронзовая втулка, 5 — ось качалки, 6 — гайка оси подвески, 7 — шайба, 8 — бронзовая втулка, 9 — косынка, 10 — передняя труба рычага, 11 — задняя труба рычага, 12 — косынка, 13 — корпус рычага.
Передняя подвеска машины — с поперечно качающимися рычагами и подрессориванием амортизаторами мотоциклетного типа. Кронштейны рычагов подвески аналогичны задним; правда, привариваются они к продольным лонжеронам рамы. Шарниры подвески оснащаются вкладышами — бронзовыми или фторопластовыми.
Реечный рулевой механизм — от мотоколяски СЗД. Поворотные вилки вырезаны из отрезков стального швеллера совместно с поворотным рычагом. Передние полуоси точеные, их размеры и конфигурация должны соответствовать штатным осям мотороллера. К поворотным вилкам они крепятся сваркой, как показано на рисунках. В неподвижные кулаки запрессованы бронзовые (можно и фторопластовые) втулки. Ось — длинный болт, посаженный плотно в вилку и по скользящей — во втулки кулаков.
Немного о технологии изготовления стеклопластиковых панелей для кузова. В принципе она несложна. Прежде всего из дюралюминиевой или стальной трубы подходящего диаметра (10…15 мм) сгибается рама, представляющая собой точный контур будущей панели, и тщательно подгоняется по линии ее разъема с остальными панелями кузова. Далее рама закрепляется строго горизонтально (например, подвешивается на четырех отрезках прочного шпагата к потолку) и к ней приклеивается «Моментом» или прихватывается нитками полотнище стеклоткани. Желательно для этой цели использовать возможно более толстую ткань — например, стеклорогожку. Операция эта весьма ответственна, поэтому советую вам не пожалеть на нее времени. Дело в том, что ткань на рамке следует закреплять не втугую, а так, чтобы она слегка провисла и образовала выпуклую поверхность двойной кривизны. Желательно контролировать себя шаблонами — особенно когда речь идет о таких больших панелях, как крыша или же крышка капота. Подтягивая или ослабляя натяжение материала, можно добиться запланированной кривизны — ведь сила тяжести в союзе с силой натяжения расположит ткань по так называемым «цепным линиям».
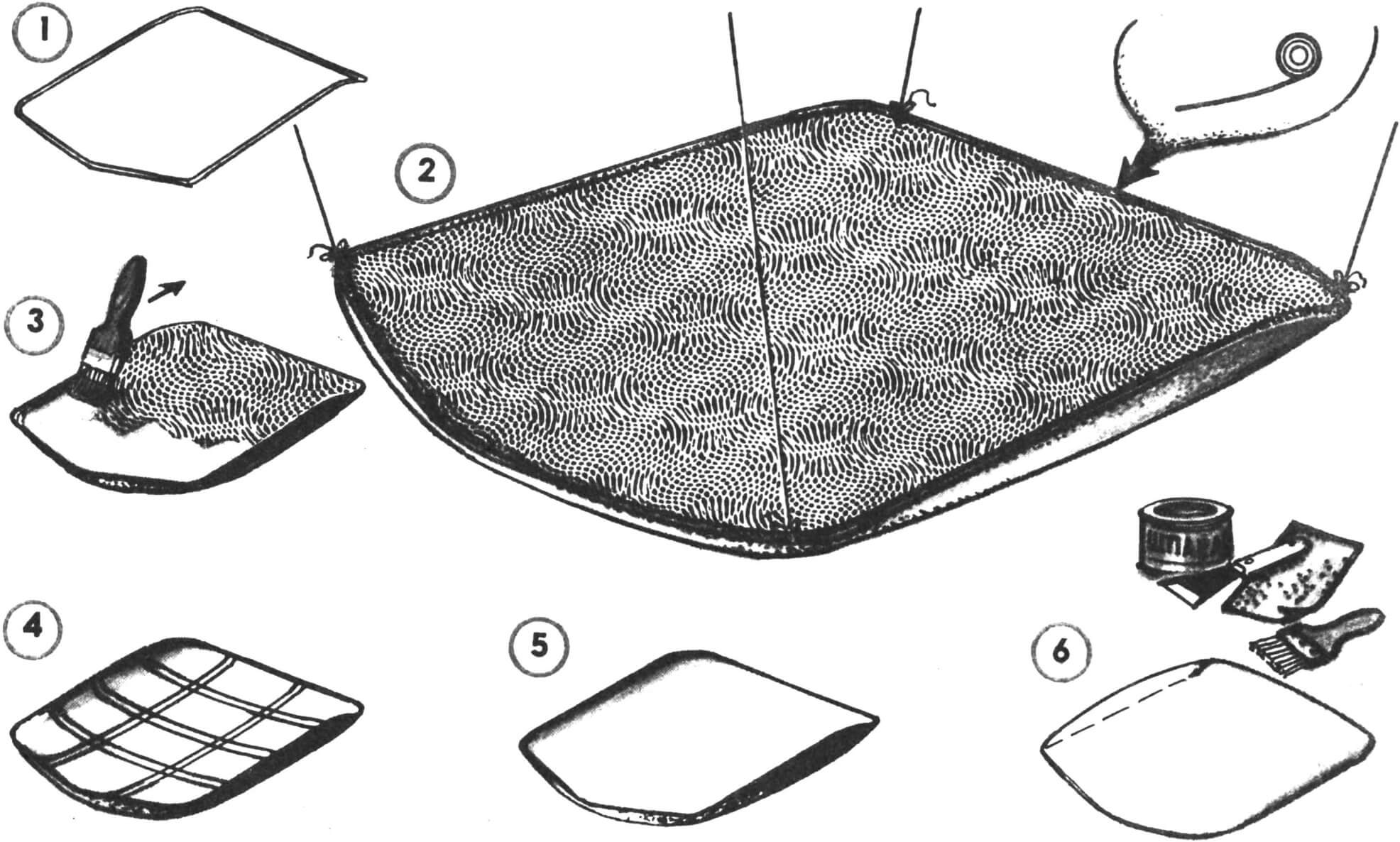
1 — изготовление трубчатой рамы, 2 — вывешивание рамы и приметывание к раме тканевой основы, 3 — нанесение на ткань эпоксидной смолы, 4 — приклеивание пенопластового заполнения, 5 — оклеивание тканью на эпоксидной смоле, 6 — отделочные операции — шпаклевание, вышкуривание, грунтование.
Теперь следует развести эпоксидную смолу с отвердителем в соотношении, указанном в инструкции, приложенной к упаковке, а затем разбавить ацетоном так, чтобы ее консистенция давала возможность воспользоваться пульверизатором. Первое «опрыскивание» должно быть таким, чтобы стеклоткань лишь слегка увлажнилась. Смоченная смолой ткань может утерять заданную форму, поэтому постарайтесь за время, пока эпоксидка не затвердела окончательно, внести некоторые коррективы в форму будущей панели.
Если возникнет необходимость создать на панели ребра или зиги, это надо учесть при подготовке каркаса, введя в него изнутри плавно изогнутые рейки (если ребро предполагается выпуклым), либо натянув снаружи одну или несколько нитей (если необходима вогнутость).
Когда первый слой частично заполимеризуется (это произойдет через 4—6 ч), нанесите на ткань еще один, и, если после этого все поры ткани окажутся закрытыми, наносите последующие слои смолой нормальной консистенции, не разводя ее ацетоном.
После этих операций оболочка приобретает, как правило, прочность, вполне достаточную для того, чтобы перейти к следующему этапу — оклеиванию панели изнутри пенопластом.
Заготовьте пенопластовую «соломку» — рейки сечением 15X30 мм. Для этого подойдет строительный или упаковочный пенопласт. Нарезать его на рейки лучше всего раскаленной электротоком нихромовой струной.
Аккуратно оклейте «соломкой» внутренность панели. Желательно при этом сначала закрепить две-четыре рейки, а когда эпоксидка отвердеет, приклеить остальные. В завершение пенопластовая поверхность выравнивается и оклеивается слоем стеклоткани.
Крепить такие панели легко за трубы каркаса, являющиеся прочной и жесткой отбортовкой — для этого в трубке засверливаются отверстия и в них нарезается резьба. Завертывать в них крепежные винты желательно также на эпоксидном клее.
Потолочная панель изнутри обтягивается декоративным материалом — тканью, дерматином или искусственной кожей.
Указанным способом можно выклеить практически все панели кузова — в том числе и заднюю дверь, и капот, и крылья, и боковые панели. По болванке формовалась лишь передняя часть достаточно сложной формы и задний бампер.
Выравнивание панелей — эпоксидной шпаклевкой. Если купить ее не удастся, замешайте эпоксидку с зубным порошком или тальком. Окончательная отделка — синтетической эмалью горячей сушки.
Сиденья в «Арбате» самодельные. Каждое представляет собой каркас из дюралюминиевых труб (от «раскладушки»), обтянутый поливиниловой трубкой. Кресло такого типа имеет хорошие амортизирующие свойства и обладает весьма малой массой. Как уже упоминалось, спинка каждого кресла может откидываться вперед, а все сиденье — поворачиваться на шарнире к борту салона. Такая его конструкция позволяет сравнительно легко попадать в салон и выходить из него через единственную дверь.
Пол в салоне выкроен из алюминиевого листа. Вблизи продольной оси на полу закрепляется кожух, внутри которого проходит втулочно-роликовая цепь трансмиссии.
Топливные баки (их два) располагаются непосредственно над двигателем, в районе так называемого «торпедо». Емкость баков 10 л — этого вполне достаточно для городской езды. Заливные горловины упрятаны под капот. Удобно воспользоваться баками заводского изготовления — например, от мопеда «Рига-11».
Приборная панель укомплектована штатным мотороллерным спидометром, контрольной лампой включенного зажигания и повторителями указателей поворота и стоп-сигнала. Смонтированы там и переключатели света фар, включатели указателей поворота и мотороллерный замок зажигания.
В заключение следует отметить, что автомобиль получился, по моему мнению, удачным — динамичным, достаточно легким, в меру скоростным, экономичным. Во всяком случае, на улице я чувствую себя водителем не тихоходной инвалидной мотоколяски, а достаточно «шустрого» автомобиля. Думаю, что среди читателей «М-К» найдутся желающие воспроизвести конструкцию моего «Арбата» — только, пожалуйста, не повторяйте «дословно». На своих ошибках вы все же чему-то научитесь, а на моих вряд ли. Да и я сегодня не спроектировал бы эту машину в том виде, в каком представил ее на страницах журнала. Но это уж размышления о будущем.
Н. ИОНОВ, инженер