Мотолодка «Мираж» укомплектована двумя веслами, изготовленными из сухой ели. После полной плотницкой обработки весла были покрыты двумя слоями горячей олифы с обязательной просушкой между слоями и окрашены водостойкой краской.
Уключины сделаны из стальных поковок с последующей слесарной обработкой и воронением. В отверстия весел и гнезда уключин запрессованы фторопластовые втулки соответствующих размеров.
Для швартовки и якорных стоянок на корпусе лодки предусмотрены четыре утки: две на топтимберсах, под уключинами, и две на корме, служащие также гнездами для лопастей весел в нерабочем положении.
Жесткость всей конструкции моторной лодки обеспечивается в совокупности ее силовым набором (килем с форштевнем, топтимберсами, флортимберсами и скуловыми кницами), носовой и кормовой палубами, подмоторной нишей, буртиками и привальными брусьями, а также технологическими элементами — зигами на плоских поверхностях, килевой, скуловыми и транцевыми отбортовками под сварные швы.
Подмоторная ниша ахтерпика сварена из отдельных панелей. В передних углах ниши встроены скобы для карабина троса, страхующего подвесной лодочный мотор от случайной потери.
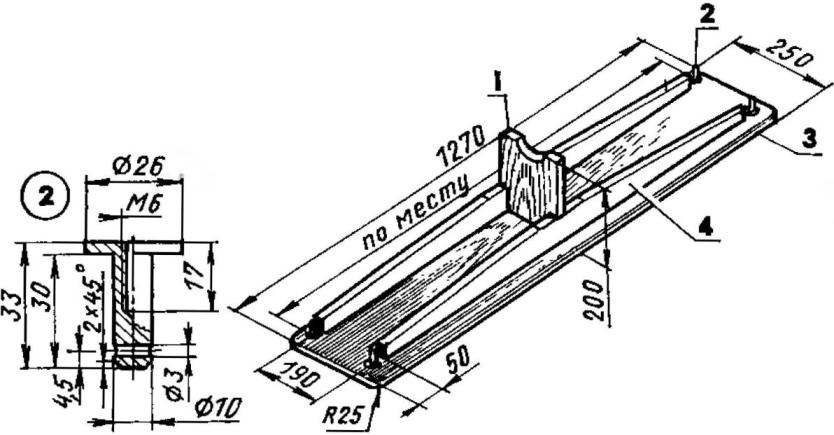
Съемная банка (вид внизу):
1 —упор (сосна, доска 190×20); 2—палец крепления (4 шт.); 3 — сиденье (сосна, доска 250×18); 4 — ребро жесткости (сосна, планка 100×10,2 шт.)
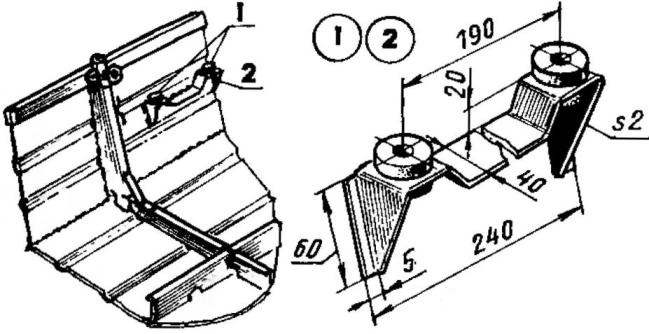
Упор съемной банки (левый борт):
1 — амортизационные втулки (резина, s20); 2 — кронштейн (сталь, лист s2)
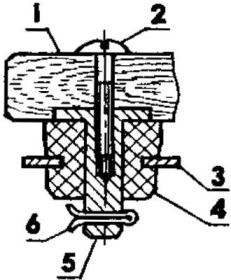
Один из четырех узлов крепления съемной банки:
1 — сиденье; 2 — винт М6; 3 — кронштейн упора; 4 — амортизационная втулка упора; 5 — палец крепления; 6 — шплинт

Весло (материал — ель):
1 — рукоятка; 2 — веретено; 3 — лопасть
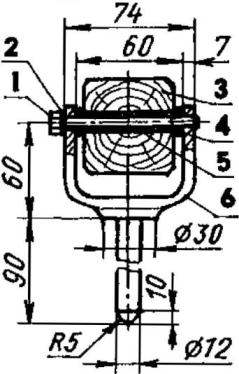
Узел установки весла:
1 — болт М8; 2 — пружинная шайба; 3 — весло; 4 — шайба (фторопласт, труба 16×4, 2 шт.); 5 — втулка (фторопласт, труба 12×2); 6 — уключина
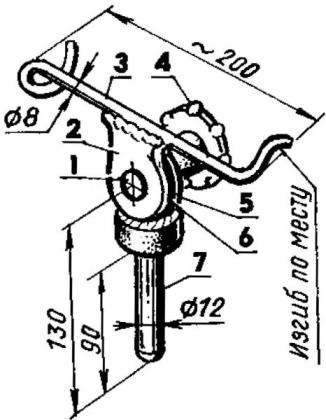
Держатель удилища:
1—болт М8; 2—фланец кронштейна (сталь, лист s5); 3 -кронштейн (сталь, пруток d8); 4 — стопорная ручка с гайкой М8; 5 — фланец пальца (сталь, лист s5); 6 — шайба (жесттсая резина, сталь s5); 7 — палец (сталь, пруток d12)
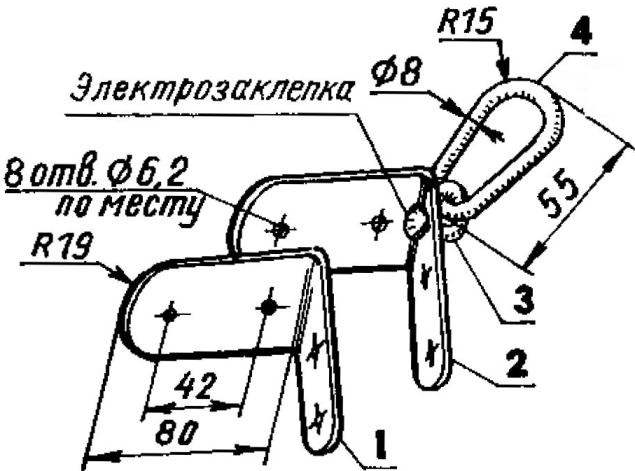
Носовое буксировочное устройство:
1 —- внутренняя накладка (сталь, лист s2); 2 — внешняя накладка (сталь, лист s2); 3 — кольцо (сталь, пруток d8); 4 — рым (сталь, пруток d8)
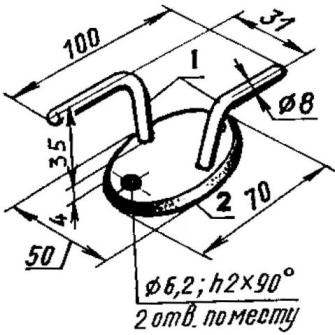
Якорно-швартовочная утка:
1 — лапки (сталь, пруток d8); 2 — основание (сталь, лист s4)
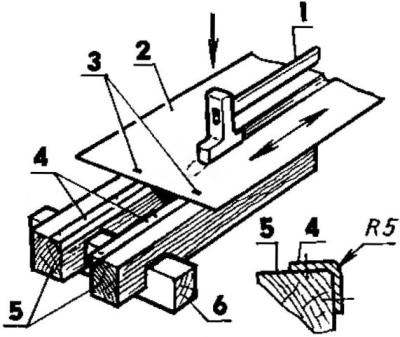
Самодельное оборудование для выколотки зигов:
1 — молоток-подбойка; 2 —обрабатываемый стальной лист; 3 — фиксаторы (гвозди); 4 — ложементы (сталь, уголок 50x50x5); 5 — продольные лаги (сосна, брус 180×180); 6 — поперечная лага (сосна, 180х 180, 2 шт.)
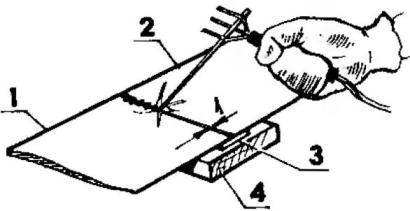
Технология сварки стальных листов встык:
1,2 — свариваемые листы; 3 — стыковая накладка (сталь, полоса 20х 1,5); 4 — подкладка (медь, полоса 60×10)
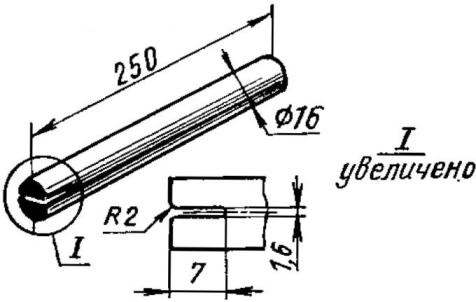
Специальный инструмент для формирования отбортовок у листовых деталей корпуса моторной лодки
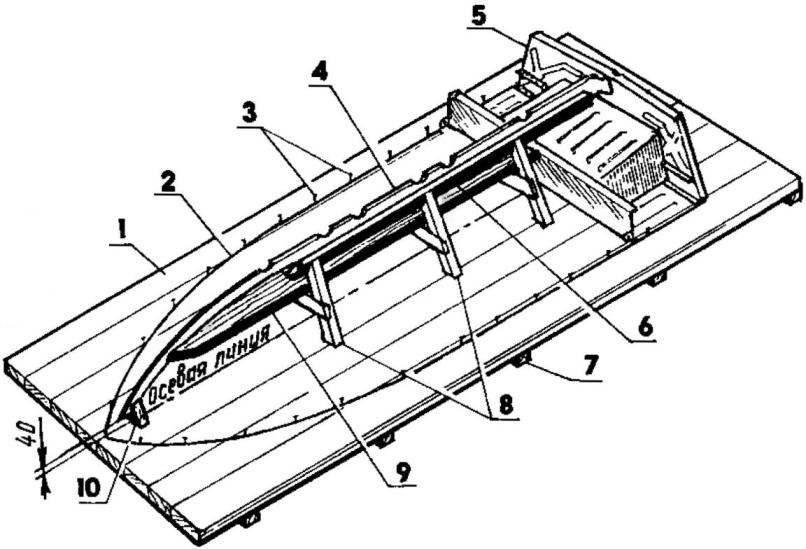
Сборочный стапель:
1 — настил стапеля (сосна, доска s40); 2 — контур борта моторной лодки; 3 — упоры-ограничители (гвозди); 4 — киль; 5 — ахтерпик; 6 — клин (сосна, брус 50×50, 2 шт.); 7 — лага (сосна, брус 180×100, 5 шт.); 8 — козлы (3 шт,); 9 — ложемент (сосна, доска s40); 10 — фиксатор форштевня (сосна, брус 180х 100)
Спереди в подмоторную транцевую доску заподлицо врезан резинотканевый вкладыш под тарелки струбцин крепления мотора, а сзади сделана накладка из бакелизированной фанеры толщиной 7 мм. Между собой весь этот пакет — вкладыш, транцевая доска и накладка — соединены шурупами и сквозными болтами М6.
Для слива воды из корпуса в транце предусмотрено отверстие с резьбовой дюралюминиевой пробкой и уплотнительным резиновым кольцом.
Кроме того, ахтерпик, как наиболее нагруженная часть корпуса лодки, снабжен множеством блоков плавучести. В частности, одним срединным (из пенопласта марки ПС-1) — между спинкой кормовой палубы и передком подмоторной ниши; двумя объемными кормовыми (из пенопласта марки ПХВ-1) — между бортами и боковинами подмоторной ниши; наконец, двумя маленькими транцевыми (из пенопласта ПС-1) — между зашивками этих блоков и транцем.
Теперь хотелось бы подробнее остановиться на технологических особенностях сборки корпуса моторной лодки.
Главная особенность заключается в том, что сначала на стапеле с помощью электросварки собирался корпус из днищевых и бортовых панелей и продольного силового набора (киля с форштевнем), а уже потом в него устанавливался поперечный силовой набор. Все детали этого набора (флортимберсы, топтимберсы и скуловые кницы) изготавливались по размерам, снятым с корпуса лодки по месту, поэтому точные их размеры на рисунках не приводятся.
Вторая технологическая особенность заключалась в том, что стальные листы, имевшиеся в моем распоряжении, не позволяли выкроить днищевые и бортовые панели целиком. Приходилось удлинять их встык, используя подкладки (стальные полоски сечением 20×1,5 мм) под сварные швы. Сварка с зазором 1 мм между листами велась на ровной медной подкладке, что исключало возможность прожога металла.
Контуры днищевых и бортовых панелей и киля с форштевнем наносились на стальные листы при помощи специальных шаблонов. Последние выкраивались по координатной сетке в натуральную величину из тонкой древесноволокнистой плиты.
Дальнейшую последовательность изготовления этих деталей покажу на примере одной бортовой панели.
Острой чертилкой я перенес с шаблона на стальной лист контур панели (он включает в себя и будущую отбортовку для сварного шва понизу). Относительно скуловой линии разметил места расположения зигов. (Для выколотки этих элементов жесткости я предварительно изготовил особое приспособление и молоток-подбойку.) Выколачивал зиги как можно аккуратнее, с небольшой вытяжкой металла за один проход по всей длине зига. Такая простая на первый взгляд работа потребовала терпения и сноровки.
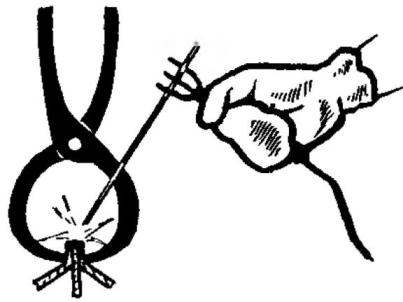
Технология точечной прихватки электросваркой:
отбортовки панелей сжимаются клещами и иа это место электродом наносится сварная точка
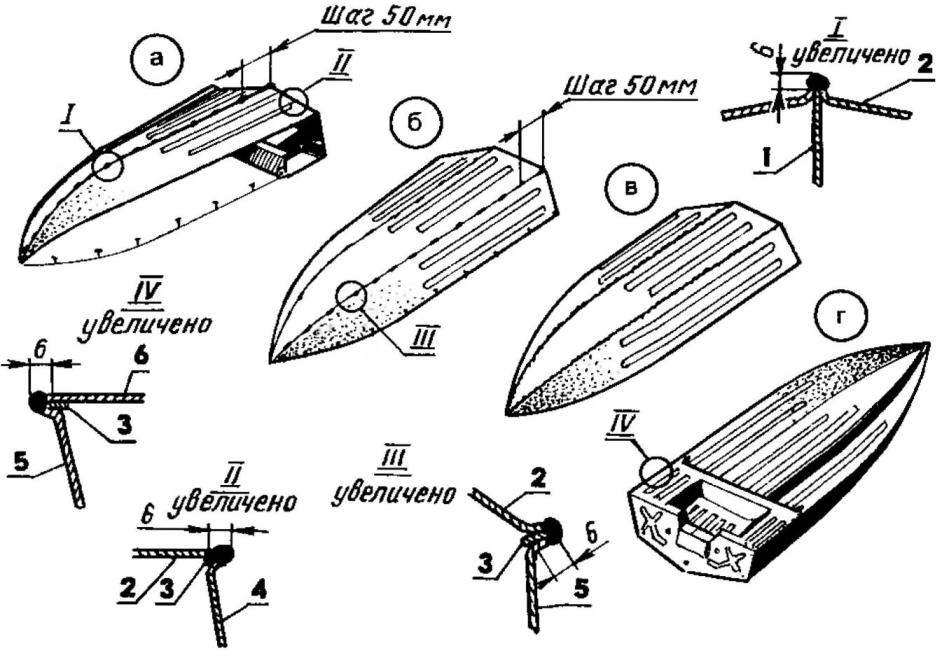
Стадии электросварочных работ по сборке корпуса моторной лодки:
а — точечная прихватка днищевых панелей к килю и ахтерпику; б — точечная прихватка бортовых панелей; в — полная сварка днищевых и бортовых панелей сплошными швами; г—-полная сварка бортовых панелей и кормовой палубы;
1 — киль; 2 — днищевая панель; 3 — прокладки (сталь, лист s 1,5); 4 —транец; 5 —бортовая панель; 6 — кормовая палуба
Выколотив оба зига, я переворачивал лист и ударами деревянной киянки правил его на ровной поверхности. Потом электроножницами как можно точнее по разметке вырезал бортовую панель. Нужно заметить, что попарно сложенные вместе бортовые (а также днищевые) панели должны были точно совпадать по контуру. Явные несовпадения я исправлял. В противном случае, нарушилась бы симметрия корпуса и усложнилась сборка.
Специально изготовленным инструментом я сделал отбортовку по скуловой линии под углом примерно 45° в сторону горба зига на всех днищевых и бортовых панелях.
Далее, собрал ахтерпик, сварив все транцевые детали и подмоторную нишу в одно целое. Затем приварил киль его кницевой отбортовкой к ахтерпику.
Окончательная сборка корпуса велась на стапеле — ровном дощатом настиле с козлами. Доски настила были побелены известью для пожарной безопасности, а потом на них нанесена необходимая разметка в виде осевой линии корпуса и контуров бортов.
На стапель я установил перевернутый ахтерпик с приваренным к нему килем, ориентируясь по осевой линии, и закрепил. Придав днищевым и бортовым панелям необходимую кривизну руками на ровном бревне, поочередно прихватил их электросваркой. При этом пользовался стальными полосками сечением 10×1,5 мм, вкладывая их между отбортовками днищевых, бортовых панелей и транца (для увеличения толщины и прочности сварных швов), а также плотницкими клещами, сжимая ими свариваемые участки.
Затем окончательно сварил корпус, применяя постоянный сварочный ток обратной полярности, подобранный опытным путем в пределах 25—90 А, и электроды диаметром от 2 до 4 мм.
Обращаю внимание на то, что все самые протяженные сварные швы находятся снаружи корпуса. Внешние швы намного удобнее варить, а их качество получается довольно высоким.
Когда швы остыли, лодку перевернул, разметил места расположения элементов силового набора и установил эти элементы, прихватывая их точками электросварки. При этом не забывал контролировать деревянным бруском, положенным поперек бортов, геометрию корпуса относительно горизонтального верха транца. Ведь даже при самом точном выполнении сборочных операций возможны погрешности — небольшие искривления и тепловые поводки.
После сварочных работ я тщательно очистил все швы металлической щеткой, обезжирил бензином, загрунтовал и окрасил все поверхности. А после окончательной сборки, установив блоки плавучести, буртики и привальные брусья, напоследок окрасил корпус моторной лодки водостойкой эмалевой краской.
В.ПЕТРОВ, Красноярский край
Рекомендуем почитать
ВТОРАЯ ЖИЗНЬ
КУБИКА... Наверное, многие не раз обжигали пальцы при пайке резисторов, трубчатых керамических конденсаторов и подобных им по форме радио-деталей. Ощущения, по себе знаю, не из...
ДВЕ ЖАРОВНИ — ТОЖЕ
Хочу поделиться с читателями несложной конструкцией домашней коптильни. Это вещь очень удобная и доступная в изготовлении, так как в ее конструкции отсутствует сварка.
Надо приобрести в...